- Published 15 Jan 2025
- Last Modified 15 Jan 2025
- 10 min
A Complete Guide to Types of Lock Nuts
Learn about different lock nut types and their applications in this comprehensive guide. Discover how they work and choose the right one for your needs.

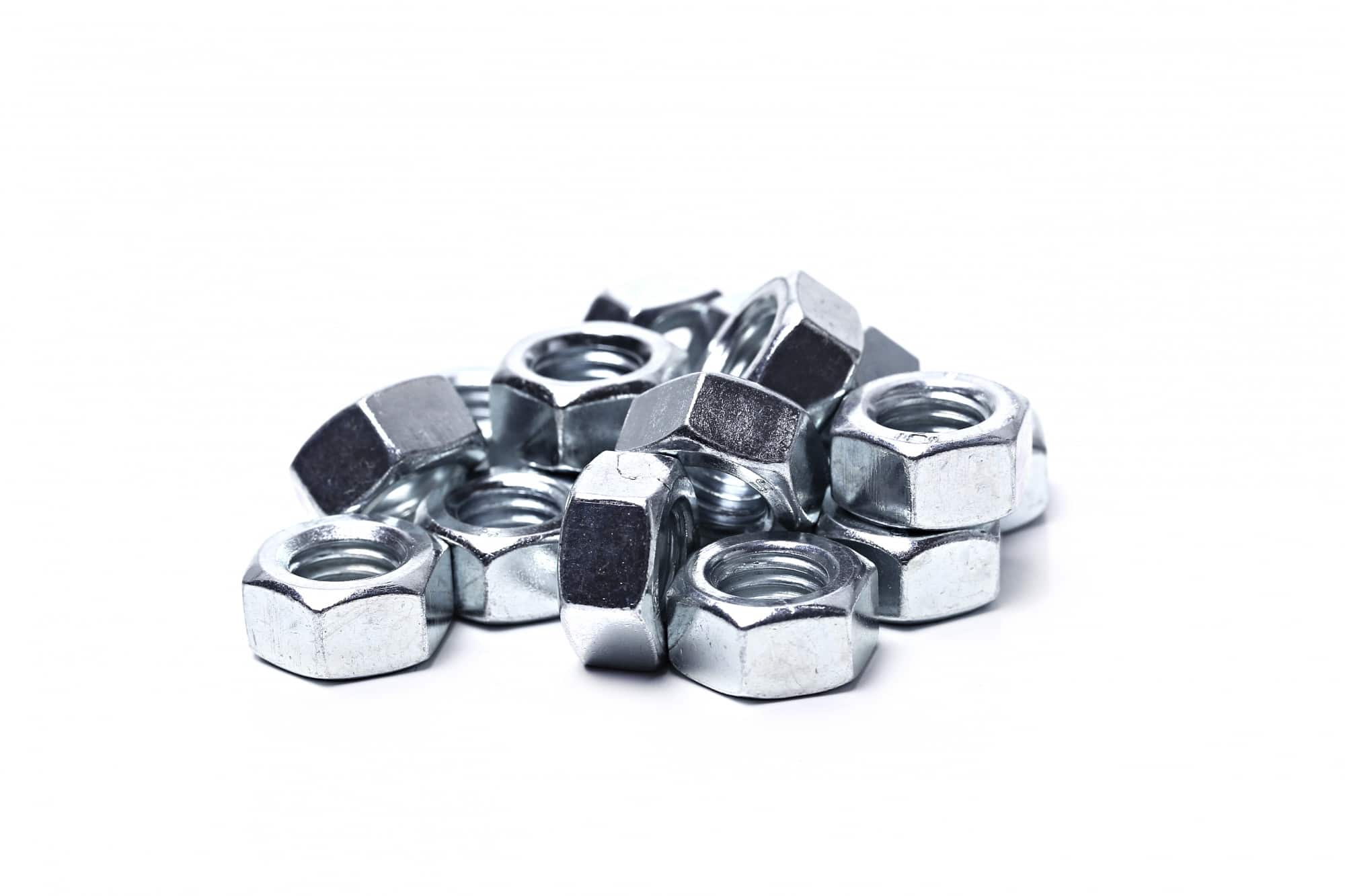
This guide delves into the different types of lock nuts, exploring their applications and best practices for installation and selection.
What Is a Lock Nut?
A lock nut, also known as a locking nut, prevailing torque nut, or stiff nut, is a specialised type of nut designed to resist loosening under vibration or dynamic loads. Unlike standard nuts, which can gradually loosen over time, lock nuts incorporate various mechanisms to maintain a secure grip on a bolt or threaded standoff. This makes them essential components in applications where vibration, movement, or safety are critical concerns, such as automotive, machinery, and construction.
Lock nuts are available in a wide range of materials, sizes, and styles to suit diverse applications. Common materials include steel, stainless steel, brass, and nylon. The choice of material depends on factors such as strength requirements, corrosion resistance, and environmental conditions.
In Australia, lock nuts are widely used in various industries and applications, including:
- Automotive: Securing wheels, suspension components, and engine parts.
- Construction: Fastening structural elements, machinery, and equipment.
- Manufacturing: Assembling machinery, tools, and appliances.
- Electronics: Securing components in electronic devices and enclosures.
As such, choosing the correct type of lock nut is crucial for ensuring the safety and reliability of your assemblies.
How Do Lock Nuts Work?
Lock nuts employ various mechanisms to prevent self-loosening and maintain a secure grip on threaded fasteners. While the specific working principles vary depending on the type of lock nut, the underlying goal is to create a prevailing torque or resistance to rotation that counteracts the forces that cause loosening.
Some common mechanisms used in lock nuts include:
- Increased Friction: Many lock nuts incorporate features that increase friction between the nut and the mating threads, making it more difficult for the nut to rotate and loosen. This can be achieved using nylon inserts, deformed threads, or specialised locking elements.
- Mechanical Locking: Some lock nuts utilise mechanical locking features, such as split beams or wedge-shaped inserts, that physically grip the bolt threads and prevent loosening.
- Adhesive Bonding: Certain lock nuts incorporate double-sided adhesive tapes or coatings that bond the nut to the mating surface, providing additional resistance to loosening.
Types of Lock Nuts & How They Work
There is a wide variety of lock nuts available, each designed with specific locking mechanisms and suited for particular applications. This section explores some of the most common types of lock nuts and how they function to prevent loosening.
Nylon Insert Lock Nuts (Nylock Nuts)
Nylon insert lock nuts, commonly known as Nylock nuts, are one of the most popular types of lock nuts. They feature a nylon insert or collar embedded within the nut, which creates a compressive force when the nut is tightened. This compression deforms the nylon insert, generating friction and resistance to rotation, effectively preventing the nut from loosening. Nylock nuts are widely used in various applications, including automotive, machinery, and electronics, where vibration resistance and secure fastening are crucial.
Hex Lock Nut
Hex lock nuts, also known as prevailing torque lock nuts, are designed with deformed threads that create a tighter grip on the bolt threads, increasing friction and preventing the nut from rotating freely. This prevailing torque resists loosening and keeps the nut securely fastened. Hex lock nuts are commonly used in applications where vibration and dynamic loads are present, such as automotive and industrial machinery.
Cage Nut
Cage nuts, also known as clip nuts or captive nuts, are designed for use in sheet metal or thin-walled applications. They consist of a nut enclosed within a spring steel cage that clips into a pre-punched hole in the material, holding the nut securely in place to prevent it from rotating or falling out. Cage nuts are commonly used in electronics, automotive, and sheet metal fabrication to attach components to thin panels or enclosures.
Locking Flange Nuts
Locking flange nuts features a built-in flange that increases the contact area between the nut and the mating surface, creating greater friction and preventing loosening. The flange also helps distribute the clamping force more evenly. Locking flange nuts are often used in applications with vibration and high clamping forces, such as automotive and industrial machinery.
All-Metal Lock Nuts
All-metal lock nuts utilise various locking mechanisms that rely on metal-to-metal contact to create a prevailing torque or physical interference that prevents the nut from rotating freely. These mechanisms include distorted threads, wedge-shaped inserts, or locking pins. All-metal lock nuts are suitable for high-temperature applications or environments where nylon inserts may not be suitable.
Split Lock Nuts
Split lock nuts, also known as slotted lock nuts, have a divided or slotted section at the top that is slightly compressed. This compression creates a spring-like action that grips the bolt threads and prevents loosening. Split lock nuts are commonly used in applications where vibration and shock are present, such as automotive and machinery.
Square Nut
Square nuts, while not strictly lock nuts, are often used in applications where self-loosening is a concern. Their square shape provides a larger contact area and increased friction, making it more difficult for the nut to rotate. Square nuts are commonly used in woodworking, furniture assembly, and other applications where a secure and non-rotating nut is required.

Which Way Does a Lock Nut Go On?
Proper installation of lock nuts is crucial for ensuring their effectiveness in preventing loosening. Here's a step-by-step guide on how to install a lock nut correctly:
1. Thread the Bolt
Begin by threading the bolt through the components you wish to join. Ensure the bolt extends sufficiently beyond the components to accommodate the lock nut and any washers.
2. Install the Lock Nut
Thread the lock nut onto the bolt. The thread orientation should match that of the bolt, ensuring it tightens in a clockwise direction.
3. Tighten the Lock Nut
Use a wrench or socket to tighten the lock nut securely. The tightening torque should be sufficient to engage the locking mechanism and prevent loosening. However, avoid overtightening, as this can damage the nut, bolt, or the components being fastened.
For different lock nut types, tighten the nylon lock nut until you feel a noticeable increase in resistance. This indicates that the nylon insert has engaged the bolt threads. Additionally, you should tighten the all-metal lock nut to the manufacturer's recommended torque specification. This ensures proper engagement of the locking mechanism without damaging the nut or bolt.
4. Ensure Secure Fit
After tightening, ensure the lock nut is securely fastened and exhibits no signs of loosening or movement. If necessary, re-tighten the nut to achieve a firm and stable connection.
By following these simple steps, you can ensure the proper installation of lock nuts, maximising their effectiveness in preventing loosening and maintaining the integrity of your assemblies.
Selecting the Right Type of Lock Nut
Choosing the appropriate type of lock nut for your application involves considering several factors to ensure optimal performance, safety, and longevity of your assemblies.
Application
The type of equipment, operating environment, and intended use play a crucial role in selecting the right lock nut. For instance, if the application involves significant vibration or dynamic loads, choose a lock nut with a robust locking mechanism, such as a nylon insert lock nut or an all-metal lock nut.
For high-temperature applications, opt for all-metal lock nuts, as nylon inserts may degrade at elevated temperatures. When it comes to corrosive environments, choose stainless steel or other corrosion-resistant materials for your lock nuts. Make sure the lock nut's thread size and pitch match the bolt or threaded fastener you use.
In Australia, some of the common applications include:
- Automotive: Nylock nuts are commonly used in automotive applications for securing wheels, suspension components, and engine parts due to their vibration resistance and reliability.
- Construction: Heavy-duty hex lock nuts are often preferred in construction for fastening structural elements and machinery due to their high strength and ability to withstand heavy loads.
- Machinery: All-metal lock nuts are suitable for high-temperature or high-vibration applications in machinery, where nylon inserts may not be appropriate.
Common Lock Nut Sizes
Australia uses metric threads categorised by their ISO (International Organization for Standardization) standards. Common lock nut sizes for Australian use include:
- M6: Used in small assemblies and electronic components.
- M8: Commonly found in machinery, automotive, and general-purpose applications.
- M10 and M12: Used for larger assemblies and structural applications.
- M16 and Above: Typically used for heavy-duty applications and large-scale machinery.
Fine & Course Threads
Lock nuts are available with both fine and coarse threads. Fine threads offer more precise adjustments and are often used in applications requiring fine-tuning or delicate assemblies. Coarse threads, on the other hand, are more common for general-purpose applications and provide faster assembly.
Choosing the correct thread type depends on the specific application and the mating thread on the bolt or fastener. Ensure the lock nut's thread matches the thread of the mating component for proper engagement and secure fastening.
By carefully considering these factors, you can confidently select the right lock nut available at RS Australia for your application, ensuring secure and reliable connections that withstand the demands of your project.
Frequently Asked Questions (FAQs)
Featured Articles
Related links
- A Comprehensive Guide to Spring Washer Uses and Applications
- A Comprehensive Guide to Solenoid Valves
- A Complete Door Bolt Guide
- Everything You Need to Know About Laminators
- A Complete Guide to Potentiometers
- The Complete Guide to Stepper Motors
- Everything You Need To Know About Thermocouples
- A Complete Guide to Microcontrollers