- Published 5 Jan 2024
- Last Modified 6 Mar 2024
- 9 min
What Is A Torque Wrench And How Do You Use It?
In our comprehensive guide, we look at what torque wrenches are and what they’re used for, as well as provided advice on how to use them and how to calibrate them for completing certain jobs.

What is a Torque Wrench?
A torque wrench is a tool used to tighten nuts and bolts to a predetermined torque value. This instrument allows fasteners to be tightened to the proper tension, helping avoid damage from over tightening or joints coming apart from under tightening. This means applying the correct torque measure is important for safety, assembly and performance of equipment.
These tools have been used since the early 20th century, having been designed in 1918 by Conrad Bahr.
What is Torque?
Torque is the measure of how much a force on an object causes it to rotate, with the pivot point being the axis the object rotates on. Torque is measured in either lb·ft (pound-foot), lb·in (pound inch), or N·m (newton meter)
What are Torque Wrenches used for?
These tools are used for a variety of different tasks across many industries – including home repairs and maintenance, automotive and construction.
It’s important to always use this tool in applications where screws and bolts must be secure and tight. These tools allow the user to measure the amount of pressure being applied to fasteners, to ensure it matches the recommended specifications for the job.
In the automotive industry, for example, it’s paramount that the right amount of torque is used for all fasteners on a vehicle, to protect the safety of everyone who comes into contact with it.
Different types and their uses
Torque wrenches are available in many shapes and sizes. The main differences between them are how they read and how easily they can be adjusted.
Here are some of the different types and what they’re commonly used for:
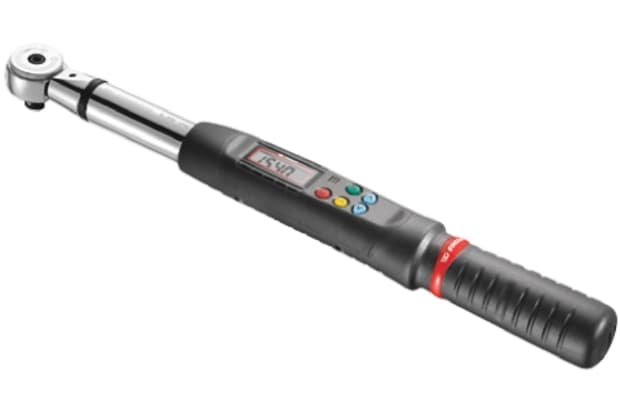
Digital Torque Wrenches
Also known as electronic, they don’t feature any moving parts and instead work from an electric sensor.
They sense how much twisting force is applied and tells the user via a digital display.
These tools include small chips which contain a memory stick to save readings, which can then be accessed on a computer
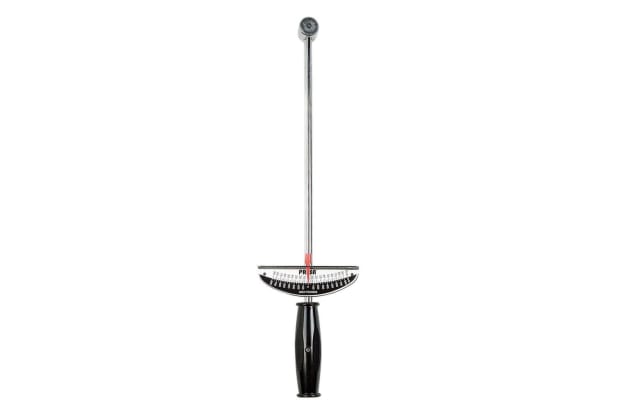
Beam Torque Wrenches
These products are generally inexpensive and easy to use. They feature a scale, and once the right level of torque has been reached it stops at the right number.
The main beam features a handle on it which is used to employ force. When in use, the beam stays in place and the scale shows the level of torque. These tools can be used for tightening or loosening.
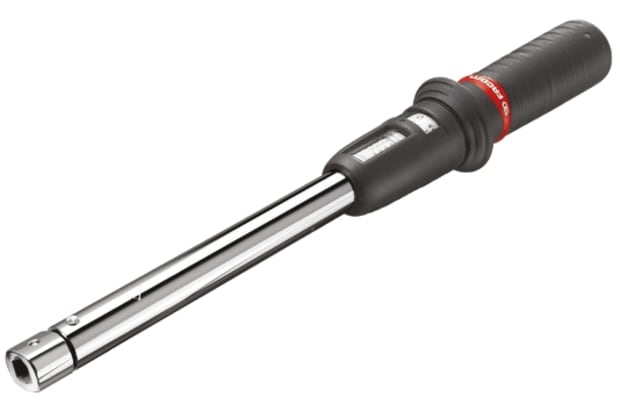
Click Torque Wrenches
A click torque wrench gives an audible sound when the correct torque setting has been reached.
This type features a spring-loaded lever which is adjusted by twisting the handle to the right setting. When the required torque level is achieved, the lever breaks which creates a clicking noise.
Most click types are ratcheting and may be used for tightening or loosening.
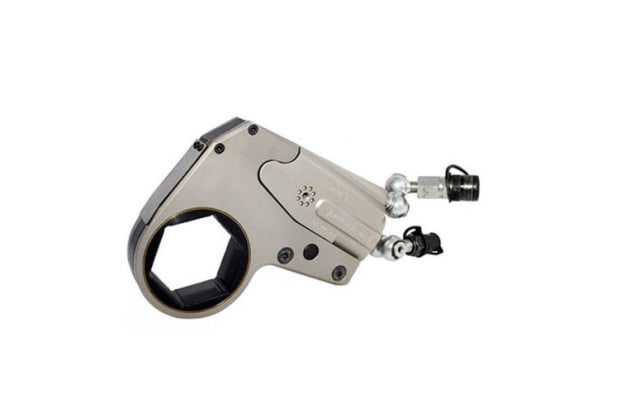
Hydraulic Torque Wrenches
This type is often used in industrial settings. They’re designed to reach the required level of torque through the use of hydraulics.
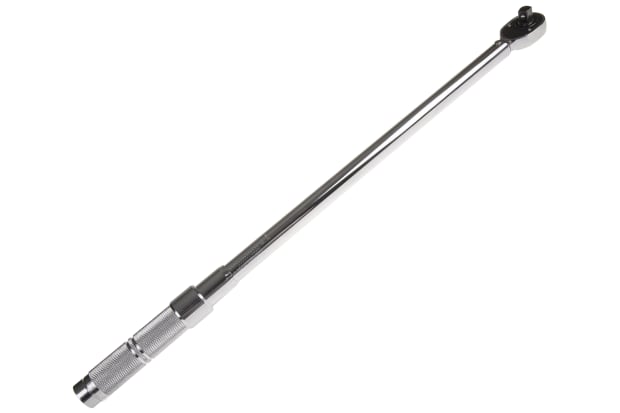
Micrometer Torque Wrenches
These scales are often used in the manufacturing and transportation of cargo. Knowing the weight of a load is vital when transporting large amounts by train, plane, or ship because the weight may change the distribution of the freight. If it’s not monitored properly, this could endanger the crew and the rest of the cargo being transported.
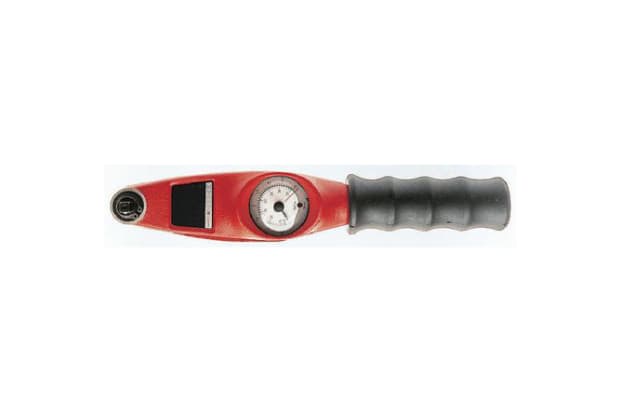
Dial Torque Wrenches
Dial torque wrenches are widely considered as one of the most accurate to use.
They can be wider than other types, so can be harder to use in small spaces.
As well as regular use in the automotive industry, these tools are used in the aerospace and defence industries.
How Torque Wrenches work
These tools are calibrated to apply a certain amount of torque to a fastener. The amount of torque that is applied depends on the amount of force on the tool’s handle and the length of the wrench. To work out the torque, the torque formula is force x length = torque.
The handle contains an internal mechanical indicator which connects to a calibrated scale. When the indicator determines the desired torque has been reached, stop twisting the bolt.
To show how much torque is being applied, the tools generally have an easy-to-read scale or display screen.
They can be calibrated to read in lb·ft (pound-foot), lb·in (pound inch), or N·m (newton meter).
How to use Torque Wrenches
It’s important to use tools which have been properly calibrated. If it’s been calibrated, it should be demonstrated with a sticker on the tool.
They often have a lock which needs to be disengaged before the handle can be rotated. Once the lock has been taken off, rotate the handle to line up the number on the handle with the centre line on the barrel. Then put the lock on to avoid any risk of adjusting the setting when using it.
When using a click torque wrench, use one hand to hold the pivot in place, then the other on the handle. Rotate the tool until it makes an audible noise. As soon as that happens, stop turning, as one click is all that’s needed otherwise the fastener can be overtightened.
Once the tool is no longer needed, position the scale back in its lowest setting, to prevent impacting its accuracy for future measurements.
Refrain from using them on fasteners which have already been completely tightened with a conventional wrench or socket, as it could be that the right level of torque has already been exceeded. Instead, it’s better to loosen the fastener then re-torque it to the right setting.
How to use a Beam Torque Wrench
These types are mostly used in automotive maintenance and repairs. Firstly, check the tool manufacturer’s manual for the recommended amount of torque for the type of fastener being adjusted; then input this measurement into the wrench's scale.
It’ll have an analogue meter showing the amount of force being applied to the bolt. Watch the gauge carefully until it reaches the desired torque level, then stop applying force to the handle.
One thing that you must take into account when using this tool is parallax. This refers to differences in the position of the needle based on the angle that it’s being looked at – so try to ensure the dial is being used at eye level.
How to set a Torque Wrench
Changing the tool’s setting can enable it to either increase torque or reduce it. To do this, turn the handle clockwise for more torque and counter-clockwise to decrease it.
Do they need to be calibrated?
To make sure torque wrenches provide reliable and precise measurements, they should be regularly calibrated.
This is the procedure of checking the accuracy of a measuring instrument – as well as the adjustment to align it with the standard. The process allows equipment to produce more accurate results than would’ve otherwise been possible.
It’s vital to regularly calibrate instruments, as their accuracy will reduce over time and with use. The permitted frame of calibration error is 5% – with any error beyond that potentially affecting the performance of the tool quite seriously, which could lead to liability for product failure.
We offer calibration for new and existing equipment, with specialists in our laboratory offering RS and UKAS-accredited services – which is recognised internationally as the industry mark of quality.
Discover more about the benefits and costs of our fast and professional calibration service.
How are they calibrated?
It’s recommended that all test and measure instruments are taken to accredited laboratories to be professionally calibrated.
Testing the tools highlights any potential problems and allows them to be fixed before they can lead to a serious issue. Calibration also ensures the user can have confidence in the accuracy of their tool and that it complies with international standards.
How often should they be calibrated?
How often this needs to be done depends largely on how frequently the tool is used, as there aren’t strict or legal time periods for having it calibrated.
It’s thought by some professionals that the performance is affected between 2,500-3,000 repetitions, so it’s recommended to have it calibrated once it reaches 2,500 repetitions.
If the tool isn’t frequently used, then around once a year is the recommended timeframe for calibration to guarantee accurate measurements.
How much torque on Spark Plugs?
When changing a vehicle’s spark plugs, always follow the instructions included in the engine manufacturer's guide to understand what level of torque is needed. Installation recommendations also vary depending on the type of spark plug – here’s a guide to help:
Thread Size | For Aluminium Cylinder Head | For Cast Iron Cylinder Head | Without a Torque Wrench |
---|---|---|---|
10mm | 8-12 lb ft | 8-12 lb ft | 1/4 turn |
12mm | 10-18 lb ft | 10-18 lb ft | 3/8 to 1/2 turn |
14mm | 18-22 lb ft | 25-30 lb ft | 1/2 to 3/4 turn |
18mm | 28-34 lb ft | 32-38 lb ft | 1/2 to 3/4 turn |
14mm taper seat | 7-15 lb ft | 7-15 lb ft | 1/16 turn (snug) |
18mm taper seat | 15-20 lb ft | 15-20 lb ft | 1/16 turn (snug) |
7/8-18 | 31-29 lb ft | 35-43 lb ft | 1/2 to 3/4 turn |
How much torque on Wheel Nuts
When tightening car wheel nuts – also known as lug nuts – it’s important to use a torque wrench as it’s commonly misbelieved that the tighter they are, the safer the vehicle is.
They're dangerous if they come loose while driving, but overtightening them can be just as dangerous.
Every car has a specified torque value for its wheel fasteners – usually in the region of 100 Nm for an average car.
Tightening the bolts more than the specified requirement will stretch them. When they’re stretched past their yield point they can shear, because the force they can usually withstand is reduced.
Using the proper torque helps ensure the wheel assembly is securely installed and following the manufacturer’s recommendations will reduce the risk of too much or too little pressure on any of the assemblies. So before installing or changing anything on a car, always check the vehicle’s specifications.
Popular Brands
For a range of high-quality torque wrenches from the most popular brands, view the full product range