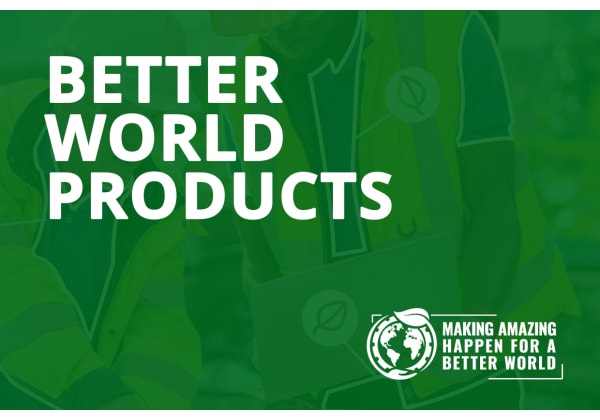
Better World Products
Want to build a better world? We do, which is why we’ve made it easier to find more sustainable products from across our product offer.
Inspiration, information and insight from RS
Want to build a better world? We do, which is why we’ve made it easier to find more sustainable products from across our product offer.
Everything you need with a full range of essential hand, from large specialty tool kits to tweezers. RS PRO covers every application in the field with an unbeatable choice of quality products. Discover the RS PRO essential selection of hand tools for engineers, electricians, mechanics and more.
We are working with market-leading partners to ensure that you access the latest technology and innovations.
We're by your side with a wide range of products to suit the demanding environments of your industry. Find the latest articles, innovative new products, service solutions and more related to your industry.
With 80+ years in electronics, we're your go-to for products, services, and design tools. From board components to displays, we've got all you need for success.
Shop 50,000+ locally stocked products for next day delivery.
Increasing Indigenous engagement is a priority for RS. The EWB and RS three-year partnership aims to not only inspire STEM, but strengthen relationships with First Nations communities.