- Published 9 Jan 2024
- Last Modified 6 Mar 2024
- 13 min
Self-Tapping Screws Guide
How to choose the right self-tapping screw for your project? Our guide explains the different options and their uses.

Reviewed by Maxwell Brown, Technical Support Engineer (April 2021)
What is a Self-Tapping Screw?
Self-tapping screws are different from traditional screws as they tap their own threads when screwed into plastic, wood, or metal. Self-tapping screws are usually split into two variants - thread forming and thread tapping.
Thread Forming Screws
A thread-forming screw has a specific thread pattern that creates a thread during insertion. As thread-forming screws tap their own thread during assembly, they do not require the hole to be tapped before insertion.
Self-Tapping Screws
Self-tapping screws are commonly used when you need to attach two pieces of material together where you can only access one side of the material. Where you can access both sides, you can use a screw or a bolt. Self-tapping screws are useful when disassembling and reassembling products such as furniture, as they will insert themselves into the same threads they have been removed from.
Self-Tapping Screws vs Self-Drilling Screws
Self-tapping and self-drilling screws can easily be confused. Self-tapping screws do not have an integrated drill bit into the screw and certain types of self-tapping screws require a pilot hole to be drilled before they can be driven into the material.
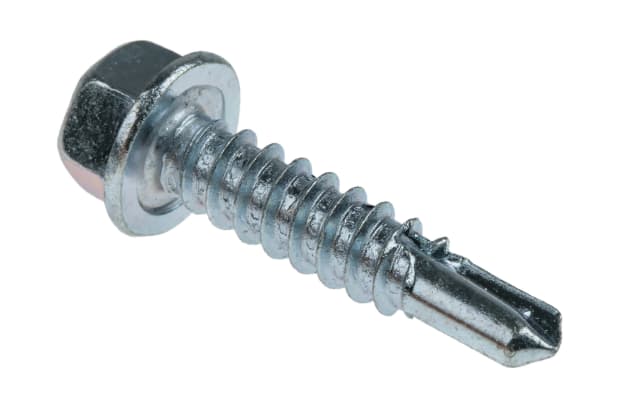
Self-Drilling Screws
Self-drilling screws are commonly used in construction, woodworking, and other applications. They differ from self-tapping screws as they drill their own pilot holes and tap threads simultaneously. They have a drill-like point with flutes or cutting edges that remove the material as the screw is driven in. The drill point creates a hole, and then the screw's threads engage the material, providing secure fastening. These screws are ideal for hard materials such as steel, aluminium, or metal alloys.
Self-Tapping Screws
Both blunt-nose and flat-ended self-tapping screws require a pilot hole slightly smaller than the screw diameter to be created before they can be driven into the material with a screwdriver. Pointed-nose self-tapping screws do not require pilot holes. The action of driving the screw in will result in the self-tapping screw cutting a thread into the material and securing the materials together. Self-tapping screws secure wood, plastic, metal and brick together.
There are two types of self-tapping screws - thread-forming and thread-cutting.
- Thread-Forming: Before you can use these screws you will need to drill a pilot hole as the screw itself does not contain a pointed tip. Thread-forming screws join plastic materials together. Due to their design, they grip materials more tightly. Care should be taken as there is a risk of over-tightening the screw, which can result in the joined materials breaking from the pressure
- Thread-Tapping: These screws do not require a pilot hole but one can be drilled to make fastening easier. Remember to make the pilot hole smaller than the thread-tapping screw diameter. Thread-tapping screws remove material and create a path for the screw. The drawback to using this type of screw is that when they are removed it can result in stripped threads. If you experience stripped threads, you should use a larger thread-tapping screw when reattachment is made
If you require Tek screws for wood applications you can use ones manufactured for roofing. The flute on these screws is very small and the diameter of the hole it drills is smaller than the diameter of the outside screw thread. This design allows the screw to bite into the material for a secure hold.
Anatomy of a Self-Drilling Screw
*Please note that wings are only present on Remer Tek screws.
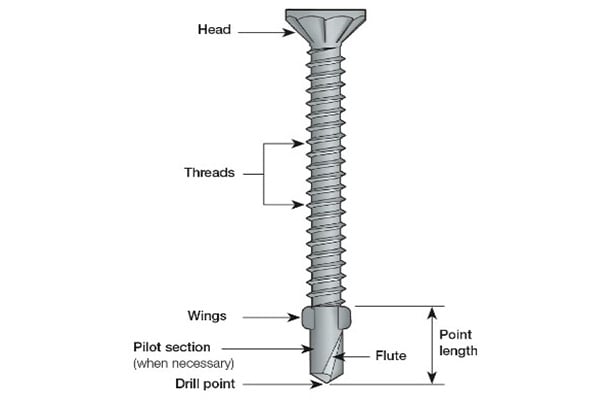
Self-Drilling Screw RPM and Force Guide
Screw Size | Major Diameter (in.) | RPM | Applied Force (lb.) | Work Material Hardness |
---|---|---|---|---|
#6 | 0.138 | 2,200 | 80 | 20 Rockwell "C" -scale |
#8 | 0.164 | 1,900 | 93 | 20 Rockwell "C" -scale |
#10 | 0.190 | 1,600 | 104 | 20 Rockwell "C" -scale |
#12 | 0.216 | 1,400 | 116 | 20 Rockwell "C" -scale |
#14 | 0.250 | 1,200 | 131 | 20 Rockwell "C" -scale |
#16 | 0.313 | 1,000 | 157 | 20 Rockwell "C" -scale |
Self-Drilling Screw Troubleshooting Guide
Failure type: Flutes chipped
Cause of failure: Too much force was used when driving the screw in
Failure type: Flute melted
Cause of failure: Too many RPMs used or the material was too hard which resulted in the flute melting
Failure type: Melted point
Cause of failure: Material too hard or too much force has been applied
Failure type: Drill bit split
Cause of failure: Too much force was used when driving the screw in
Failure type: No drilled hole
Cause of failure: Multiple reasons for failure include too hard material, the driver set to reverse, or the drill point is blunt which could be due to handling or a manufacturer defect
What Should You Consider When Deciding Which Self-Tapping Screw to Use?
Self-drilling screws are available in the same head and drive types as self-tapping screws. You should select your screw type based on the material and finish you require. Below we have outlined some factors to consider when selecting.
- Flute Length – The length of the flute determines the thickness of the metal that a self-drilling screw can be used on. The flute is designed to extract the drilled material from the hole. Cutting will cease if the flute becomes blocked. Simply put, if you attach thick pieces of material, you will need a self-drilling screw with a flute to match. If the flute becomes blocked and you take no action the drill point will likely overheat and fail
- Drill Point – The drill point refers to the unthreaded section of the screw. When selecting the screw length, you should account for the length of material you are drilling through. If the threads engage before the drill point length is completely through the material it will result in the screw breaking
- Winged and Non-Winged – It is necessary to use self-drilling screws with wings when fastening wood over 0.5 inches thick to metal. The wings will ream a clearance hold and keep the threads from engaging too early. When the wings engage with the metal they will break off, allowing the threads to engage in the metal. If the threads engage too early this will separate the two materials
Self-drilling screws are susceptible to the same forces as drill bits. Cutting performance is impacted by the speed and depth of the cut. Make sure to select the correct size screw for your application. This will avoid the drill head melting if too much RPM is applied or snapping if too much pressure is applied. A simple rule of thumb is that small diameter screws can take higher RPM but less force can be used. Transversely, the larger the diameter the lower the RPM, but higher force can be applied.
Popular Types of Self-Tapping Screws
Common Project Questions
Self-Tapping Screws for Aluminium
Aluminium has many positive characteristics that make it easy to work with. When using self-tapping screws on aluminium, choose a self-tapping screw with a drill-like point and sharp cutting blade threads that extend down the whole length of the screw. These self-tapping screws are designed to keep thin metal from denting.
To use self-tapping screws, place the screw directly on the aluminium sheet. The screw's sharp point will make its own hole. Stabilise the screw so it doesn't tilt as it is put in. Let the screw turn until it goes through. Take care not to over-tighten the screw as this can damage the metal or break the screw.
The advantage of self-tapping screws for aluminium is that they don't need pre-drilling and are easily removed without damaging the metal. They can also be reused in the same material.
Aluminium in certain applications can vibrate which causes other fastener types to work loose. For example, aluminium is used to build boats. Boat engines cause the boat frame to vibrate which can result in other fasteners such as nails or regular screws falling out. Trilobular stainless steel self-tapping screws are ideal in situations where vibration is present as their thread design reduces friction during thread forming whilst providing resistance to vibrational loosening.
Self-Tapping Screws for Plastic
Plastics are more ridged than wood and more prone to cracking. When using self-tapping screws in plastic it is advised that you drill a pilot hole before screwing in the self-tapping screw. If you are installing hardware such as hinges on plastic you will want to avoid drilling the pilot hole fully through the material for aesthetic reasons.
UPVC Window Screws
UPVC window screws are available in a variety of lengths but typically come in one diameter (4.8mm gauge). Standard UPVC hardware screws are between 3.9mm and 4.3mm thick. To ensure a tight fit when reattaching window furniture, extra thickness is added to UPVC screws to ensure a secure fit and material for the screw to bite into.
Self-Tapping Screws for Fibreglass
Fibreglass consists of glass fibres embedded in resin. The combination of glass fibres and resin makes for a very strong material. When using self-tapping screws in fibreglass, you will find that the drilling tip of the screw becomes dull quickly as it comes into contact with the glass fibres, which leads to cracking in the glass fibres and the gel coat. To avoid cracking, proper installation techniques must be used.
FAQs
Related links
- Self Tapping Screws
- Self Drilling Screws
- RS PRO Steel Phillips Head Self Tapping Screw
- RS PRO Truss Head Self Tapping Screw, 5/8in Long
- Hammond Self Tapping Screw
- RS PRO Plain Stainless Steel Pan Head Self Tapping Screw, N°10 x...
- RS PRO Plain Stainless Steel Countersunk Head Self Tapping Screw,...
- RS PRO Pan Head Self Tapping Screw, 3/4in Long