- Published 19 Apr 2024
- Last Modified 19 Apr 2024
- 6 min
Overcoming Common 3D Printing Challenges with ABS Filament
Learn how to overcome warping, cracking, adhesion issues and other common 3D printing failures. Achieve superior prints with RS Australia's ABS filaments.

Acrylonitrile Butadiene Styrene (ABS) filament is a popular 3D printing material favoured for its superior strength, durability and high-temperature resistance compared to its counterpart, Polylactic Acid (PLA). Commonly used in creating everything from durable consumer goods and automotive parts to protective housings for electronic devices, ABS filament is a versatile material suitable for a wide range of applications.
Despite its popularity among 3D printing enthusiasts and professionals, working with ABS filament comes with its unique set of quirks and challenges that can frustrate even the most experienced printers. Warping, cracking, and adhesion issues frequently mar the printing process, turning promising projects into failed attempts. This guide seeks to demystify these common challenges, offering tried-and-true strategies to overcome them, paving the way for consistently successful ABS prints.
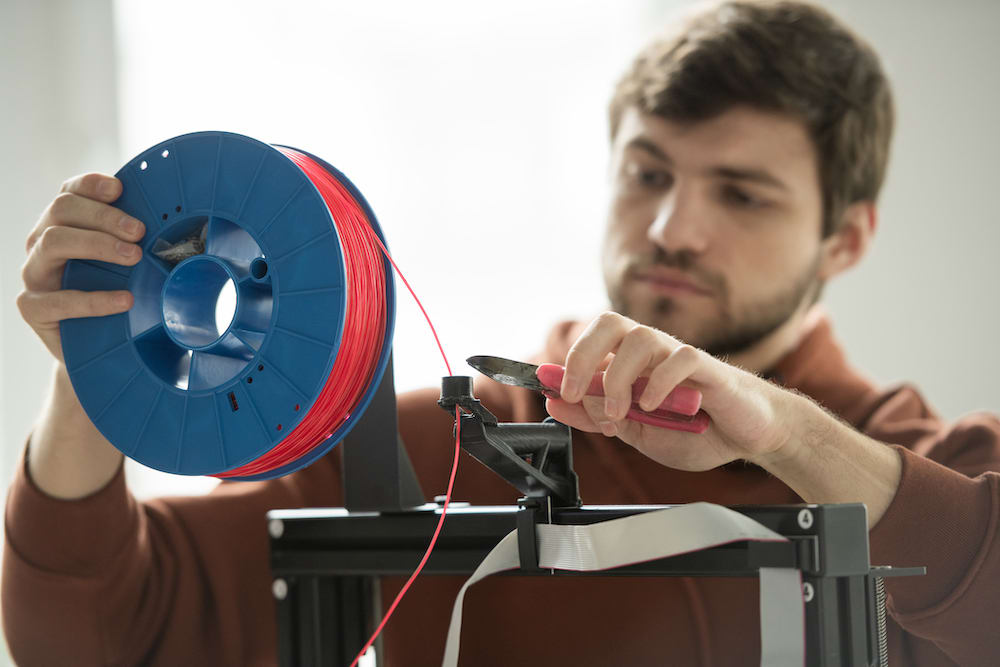
Understanding the Properties of ABS Filament
ABS is a thermoplastic polymer that combines three distinct monomers: acrylonitrile, butadiene, and styrene, each contributing unique properties to the final material. The chemical structure of ABS is the key to its notable physical and mechanical characteristics, particularly its high tensile strength and stiffness.
- Acrylonitrile: Provides ABS with its high thermal stability and chemical resistance. The polar nitrile groups in acrylonitrile form strong intermolecular attractions between polymer chains, leading to increased rigidity and strength. This component is crucial for the material’s performance in high-temperature applications.
- Butadiene: A rubbery substance that imparts toughness and impact resistance to ABS. The long, flexible chains of butadiene introduce elasticity, allowing ABS to absorb and dissipate energy without fracturing, contributing to its durability under mechanical stress.
- Styrene: Offers good processability and a shiny surface finish, contributing to the aesthetic qualities of ABS. The benzene rings in styrene provide rigidity to the polymer, enhancing its stiffness and structural integrity.
The combination of these monomers results in a copolymer with a tough, rubbery phase within a rigid framework. This enables ABS filament to maintain its shape and structural integrity under load with enough elasticity to resist breaking under impact. This makes it an ideal choice for 3D printing applications requiring durable yet somewhat flexible materials.
Common Challenges When Using ABS Filament for 3D Printing
There are many advantages to working with ABS filament, but the material also comes with its own set of challenges that can hinder the 3D printing process. Understanding these common 3D print failures is the first step towards mitigating them and achieving high-quality prints. Here, we’ll explore some of the most common issues faced when printing with ABS filament and the underlying reasons for these problems.
- ABS Warping and Cracking: One of the most common reasons for 3D print failures is ABS warping and cracking. 3D print warping occurs when the corners of the print lift off the print bed, while cracking occurs when layers separate during or after printing. These issues stem from the ABS material’s tendency to contract as it cools. As the bottom layers of a 3D print cool and contract faster than the upper layers, this differential in contraction rates can lead to distortions or fractures in the print, compromising its integrity and appearance.
- Poor Bed Adhesion: Ensuring the first layer of a print is adequately adhered to the print bed is critical for successful 3D printing. However, ABS filament can sometimes struggle to stick to the print bed, leading to prints that shift or detach midway through the printing process. This makes it difficult to achieve a stable foundation for the print, resulting in failure or poor-quality prints.
- Air Quality Concerns: The process of 3D printing with ABS filament can emit unpleasant odours and release volatile organic compounds (VOCs) into the surrounding environment. These emissions can be concerning in areas with insufficient ventilation, posing potential health risks to individuals in close proximity to the 3D printer.
Industries involved with 3D printing parts should observe the workplace exposure standards for airborne contaminants outlined by Safe Work Australia in order to ensure the health and safety of employees.
Solutions to Overcome ABS 3D Printing Challenges
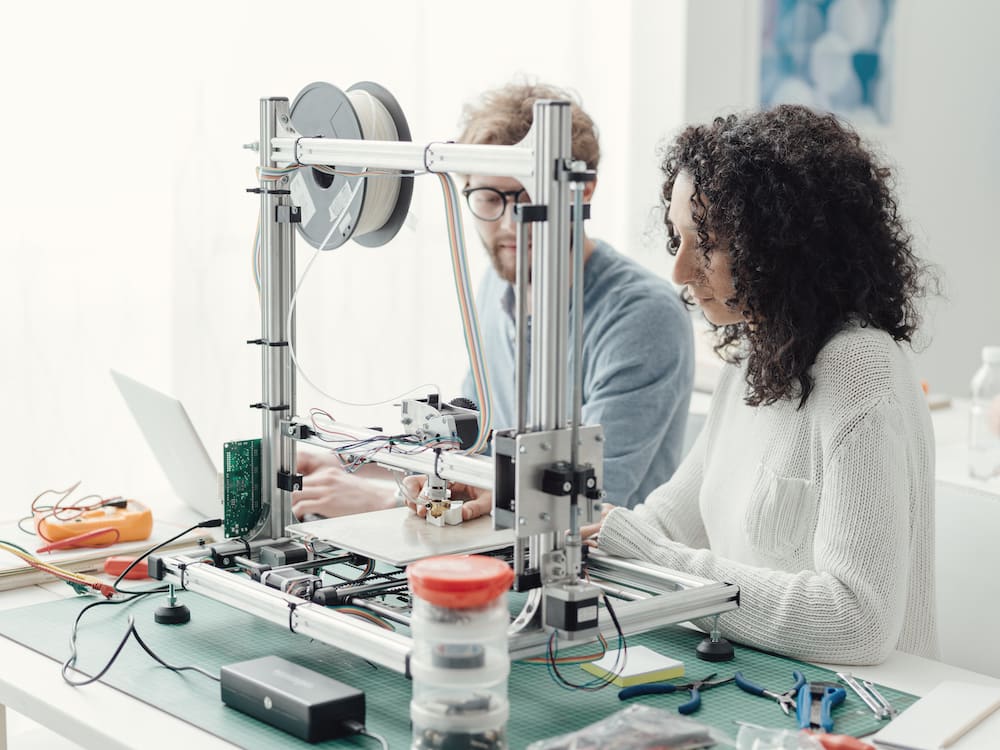
Overcoming 3D printing challenges with ABS filament is all about working around its propensity for warping, cracking, and other issues. By making adjustments to the printing environment, it's possible to avoid these common 3D print failures and achieve high-quality prints.
Optimising the 3D Printing Environment
- Heated Print Bed: Use a heated print bed to improve first-layer adhesion and reduce warping. The heat helps maintain the initial layers at a temperature closer to the ABS melting point, preventing premature cooling and contraction.
- Enclosed Printer: If possible, use an enclosed 3D printer capable of maintaining a consistent temperature around the print, slowing the cooling rate and reducing thermal stress on the material.
Adhesion Techniques and Bed Preparation
- Use Adhesives: Applying an ABS slurry (a mixture of ABS filament dissolved in acetone), hairspray, or glue sticks to the print bed can help the first layer adhere to the print bed, preventing the print from shifting or detaching.
- Bed Levelling and Surface: Make sure your print bed is properly levelled to ensure uniform contact between the first layer and the 3D printing surface. Choosing an appropriate bed surface, such as PEI sheets or glass, can also improve adhesion and make for easy print removal once cooled.
Improving Print Quality
- Temperature, Speed, and Cooling Adjustments: Fine-tuning the printer's settings, including the nozzle temperature, print speed, and cooling fan operation, can mitigate ABS warping or cracking. A slightly higher nozzle temperature and lower cooling speed can promote better layer bonding and reduce internal stresses.
Health and Safety Measures
- Ventilation Solutions: Given the potential emissions of unpleasant odours and VOCs when 3D printing with ABS filaments, it is important to ensure adequate ventilation. Using an enclosed printer equipped with a built-in filtration system can significantly reduce exposure to these emissions. Alternatively, consider installing extractor fans or choose a suitable air quality monitor to be mounted in 3D printing areas to maintain air quality and safety standards.
Achieve High-quality 3D Prints with ABS Filaments from RS Australia
While 3D printing with ABS filament can be challenging at times, it’s possible to consistently achieve high-quality prints once you understand the properties of the material. By applying the solutions outlined in this article, from optimising the printing environment to employing specific adhesion techniques, printers can avoid common 3D print failures associated with the ABS material.
Unlock the potential of your 3D printing projects with RS Australia's premium selection of ABS filaments. Explore the range today to experience the difference high-quality 3D printing filaments can make in your projects.
Related links
- 3D Printing Materials
- RS PRO 1.75mm Blue ABS 3D Printer Filament, 1kg
- RS PRO 2.85mm Silver ABS 3D Printer Filament, 1kg
- RS PRO 1.75mm Black ABS 3D Printer Filament, 300g
- RS PRO 1.75mm Orange ABS 3D Printer Filament, 1kg
- RS PRO 1.75mm Yellow ABS 3D Printer Filament, 1kg
- RS PRO 1.75mm Silver ABS 3D Printer Filament, 1kg
- RS PRO 1.75mm Red ABS 3D Printer Filament, 1kg