- Published 19 Apr 2024
- Last Modified 19 Apr 2024
- 9 min
Inductive Sensors for Quality Control in Manufacturing
Explore how inductive proximity sensors help with manufacturing automation and improve efficiency by detecting metallic objects without physical contact.

As the manufacturing industry continues to evolve, the reliance on automation technologies to streamline production processes and bolster operational capabilities has become essential. Among these technologies, inductive sensors are indispensable in advanced proximity detection.
Integrating inductive sensors in your manufacturing operations may help minimise human intervention and reduce the likelihood of errors and accidents. As such, companies can work on improving operations and output through automation while still aligning with manufacturing and processing standards set by the Australian Government.
Through the strategic integration of inductive sensors, manufacturers are equipped to navigate the complexities of modern production demands while maintaining the highest levels of quality and safety.

Understanding Inductive Sensors
Inductive sensors operate on the principle of electromagnetic induction to detect metallic objects without requiring physical contact. This is achieved by generating an oscillating electromagnetic field around the sensor's face, which is disrupted when a metallic object enters its vicinity. This disruption alters the field's properties, triggering the sensor to output a signal. This non-invasive approach allows for precisely identifying object proximity, making these sensors invaluable in automating assembly lines and quality control processes.
Types of Inductive Sensors and Their Applications
Inductive sensors are categorised based on their power supply type, each designed to suit specific applications. The main types are AC and DC-powered sensors, distinguished by their voltage requirements and operational characteristics.
AC-Powered Sensors
AC-powered sensors typically operate within 90 to 240 volts, varying by brand and model. They excel in activating small inductive loads such as contactors and relays without significant electromagnetic interference. Additionally, these sensors can operate directly from an AC power source without needing a converter, simplifying their installation and use.
These inductive proximity sensors are typically used in heavy industrial machinery where the power is readily available and preferred for robustness. Ideal for environments where sensors need to directly control large inductive loads, such as motors, contactors, and relays, without additional relay systems or converters.
DC-Powered Sensors
DC-powered sensors are designed to operate with a voltage supply ranging from 5 to 35 volts. Due to the sensor’s polarity sensitivity, the correct connection of positive and negative wires is crucial for their operation. Moreover, they are designed to seamlessly integrate with various types of PLCs and counters, making them versatile for numerous applications.
With lower voltage operations, DC-powered sensors are suited for precision equipment manufacturing, where fine control and lower power consumption are desired. These sensors are commonly used in systems requiring integration with programmable logic controllers (PLCs) and digital counters, thanks to their compatibility and ease of integration with electronic control systems.
Shielded vs. Unshielded Sensors
Aside from their power supply type, inductive sensors are also classified into shielded (flush) and unshielded (non-flush) types based on their internal structure and electromagnetic field behaviour.
- Shielded (Flush) Sensors: These sensors are equipped with a metal shield that focuses the electromagnetic field to radiate primarily from the face of the sensor. This design allows them to be mounted flush with metal surfaces without triggering false activations.
- Unshielded (Non-Flush) Sensors: Without a metal shield, the electromagnetic field of these sensors extends more broadly, radiating from the sides as well as the face. This broader field pattern prevents flush mounting in metal brackets, as the surrounding metal would trigger the sensor.
Key Differences:
- Switching Distance: Unshielded sensors typically offer a longer switching distance than their shielded counterparts.
- Switching Frequency: However, shielded sensors generally achieve higher switching frequencies.
2-Wire vs. 3-Wire Sensors
- 2-Wire Sensors: These sensors have two connecting wires and operate by connecting the load in series with the sensor. The sensor's operation allows for a minimal current flow through a resistor when off, powering the sensor itself and generating a voltage across the sensor when activated. They are available as either normally open or normally closed types.
- 3-Wire Sensors: Featuring three wires, two for power connection (brown for positive and blue for negative, following the European standard EN 50044) and one black wire for output. These sensors can be either NPN or PNP type, distinguished by their transistor operation.
- NPN Sensors: The current flows from the base to the emitter when powered, allowing current from the collector to the emitter. Their output switches from high to low when a metallic object is detected within range.
- PNP Sensors: Conversely, in PNP sensors, current flows from the emitter to the base to activate the sensor, with the output behaviour opposite that of NPN sensors.
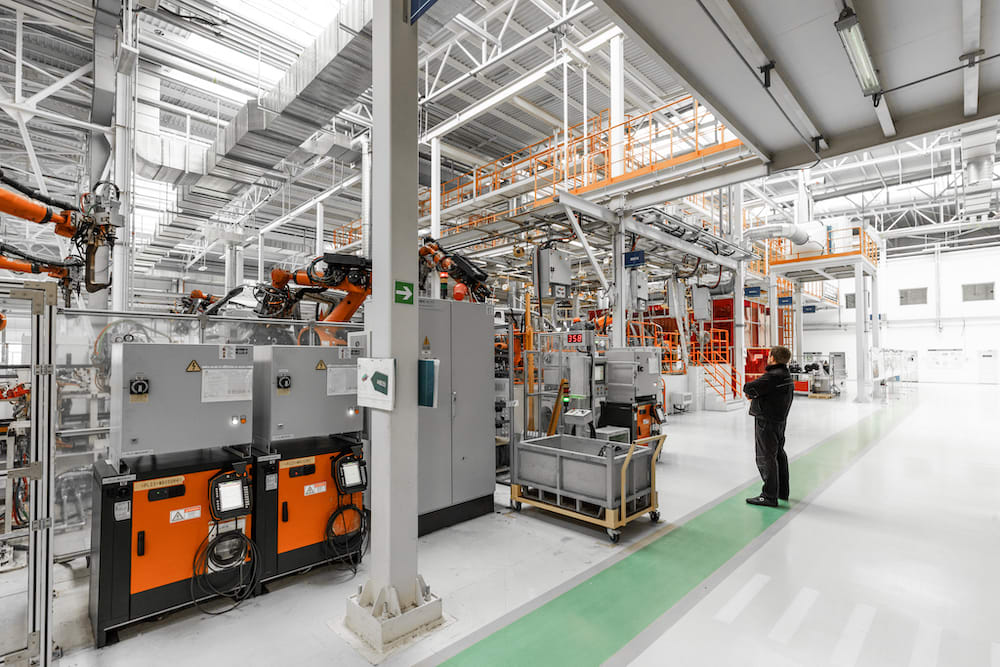
Implementing Inductive Sensors in Manufacturing
Integrating Inductive Sensors with Manufacturing Systems
The introduction of inductive sensors into manufacturing setups offers transformative potential for automation, accuracy, and efficiency. Achieving this necessitates a structured approach from initial assessment to full-scale deployment. Here's how:
- Assessment and Planning: Begin by evaluating your manufacturing environment to identify critical points where inductive sensors could add value—be it on conveyor belts for detecting item presence, within assembly lines for precision positioning, or alongside robotic arms for ensuring operational safety.
- Selecting the Right Sensors: With a clear understanding of your needs, select the appropriate inductive sensors. Determine the sensing distance required, the environmental conditions (e.g., exposure to fluids or extreme temperatures), and the types of materials the sensors will detect.
- Design and Integration: Develop a detailed plan for integrating the sensors into your system. This includes determining their exact placement, wiring them into your control systems, and programming any necessary logic to process their signals. Moreover, consider how the sensors will interact with existing equipment and whether any modifications are necessary.
- Testing and Evaluation: Before going live, rigorously test the integrated proximity sensors within your manufacturing processes. Look for any inaccuracies or inefficiencies and adjust the setup accordingly. This step ensures that the sensors are fully functional and meet your operational requirements.
Optimising for Efficiency
To leverage inductive proximity sensors for maximum benefit, their strategic placement and configuration are crucial. Optimisation tips include:
- Strategic Sensor Placement: Place sensors at points where they can best detect the presence or absence of materials or products without interference. Ensure there's no obstruction that might hinder their performance.
- Configuration for Maximum Accuracy: Adjust sensor settings for the optimal balance between sensitivity and specificity. This minimises false positives and negatives, ensuring that the sensors accurately reflect the state of your manufacturing processes.
- Integration for Real-Time Responsiveness: Seamlessly integrate sensors with your manufacturing control systems to allow for real-time adjustments based on sensor input. This could mean stopping a conveyor belt if a product is missing or out of place, thereby reducing waste and improving efficiency.
Maintenance and Calibration
Ensuring the long-term reliability and accuracy of inductive sensors involves regular maintenance and calibration. Best practices include:
- Routine Inspections: Implement a schedule for regular inspections of your sensors. Look for signs of wear, environmental damage, or any factors that could compromise sensor functionality.
- Regular Cleaning: Keep the sensor faces clean and free from debris. Accumulation of dust or particles can affect the sensor's ability to detect objects accurately.
- Periodic Calibration: Conduct calibration checks to ensure sensors are operating within their specified range. Use known standards to verify their accuracy and make adjustments as needed.
- Documentation and Tracking: Maintain detailed records of maintenance activities, calibration results, and any issues identified during inspections. This helps not only with troubleshooting but also with planning for future sensor needs or upgrades.
Integration of Inductive Sensors with IoT and Industry 4.0
Merging inductive sensors with IoT (Internet of Things) and Industry 4.0 can transform manufacturing operations into a smarter, more efficient process. These sensors, when connected to a network of devices and machinery, provide real-time insights that can be used to improve production lines, forecast maintenance, and boost overall productivity. This combination allows for manufacturing adjustments in real-time, based on sensor data, leading to more informed decision-making and constant identification of ways to enhance efficiency.
Inductive switch sensors also contribute significantly to safety and quality in Industry 4.0 settings. They offer accurate data on component positioning, helping to reduce downtime and waste, and are key to predicting maintenance needs, as well as preventing failures before they occur. This proactive approach saves costs and prolongs the life of machinery. By analysing sensor data within IoT and Industry 4.0 frameworks, manufacturers gain the ability to refine operations rapidly and innovate in response to market changes, highlighting the power of integrating inductive sensors with modern digital technologies for a smarter manufacturing future.
Find Inductive Sensors to Enhance Your Manufacturing Systems at RS AU
RS Australia offers a vast selection of inductive sensors tailored for manufacturing firms aiming to boost their production efficiency through automation and adhere to compliance standards. Check out our extensive collection of inductive proximity sensors designed to enhance your manufacturing lines today. We also offer other components and equipment for your manufacturing systems, such as electric motors and motor controllers.
If you want more insight into tools and components used in industrial settings, check out our guide on temperature controllers and introduction to micrometers.