- Published 24 Apr 2024
- Last Modified 24 Apr 2024
- 14 min
The Complete Guide to Hole Saws

In this guide, we’ll cover how a hole saw works, offer a few basic tips on how to use a hole cutter bit properly, and also look in more detail at some of the many different versions of job-specific hole saws you can buy on today’s market.
What are hole saws?
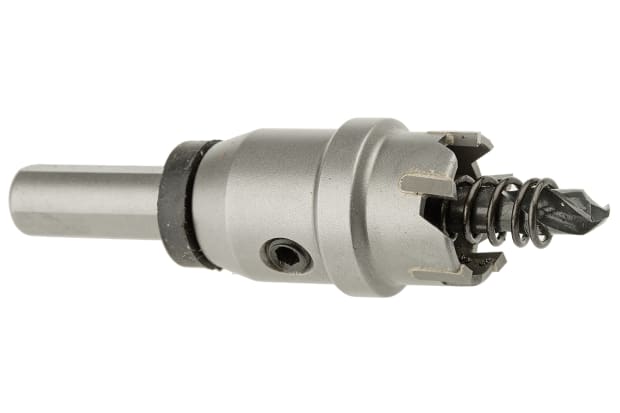
A hole saw or hole cutter is a specialist type of drill bit, designed to allow the user to bore out a circular hole of wider diameter than most standard bits would typically create.
Available for purchase in single units or as part of a multi-piece hole saw set, these types of hole cutters are highly versatile and commonly used items of DIY kit. They’re generally quite inexpensive and widely available, and they feature prominently in both professional and hobbyist tool boxes across a broad range of industries and applications.
Many different types of hole saw bits are available from a wide range of hardware stockists - almost as many varieties as normal drill bits, in fact - including versions manufactured for use on most sorts of sheet materials. In addition to general purpose hole cutting attachments, especially common variants of hole saws include models explicitly intended for:
Ceramics and tile
Most types of masonry, including brick, concrete and stone
Glass and enamels
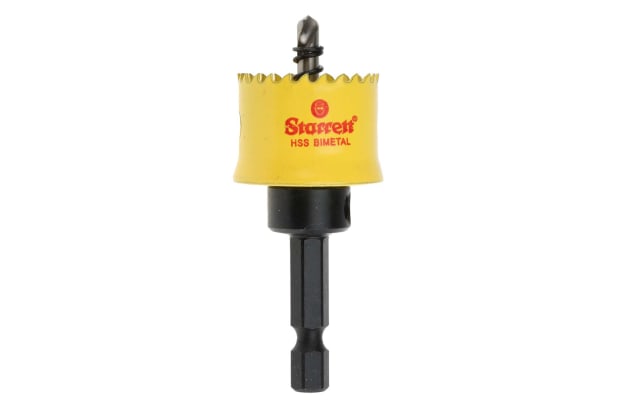
As noted above, hole cutters are very common everyday toolkit items, and you’ll see numerous brands of hole saw widely available from the majority of suppliers that offer a range of drill bits for individual purchase or wholesale.
The most familiar style of hole saw you’ll generally find in product catalogues is based around the standard cylindrical metal tube, with a shank at one end for insertion into a drill chuck. The boring edge usually consists of a circular arrangement of sharp teeth, machined around the full perimeter of the open cutting end of the bit.
Some hole saw designs also feature an arbor or pilot bit (either built-in or removable), which protrudes through the hollow centre of the hole cutter. They help to align and steer the hole cutting tool as it descends through the workpiece, and in many scenarios these handy additions can eliminate the need to drill a preliminary pilot hole before making the main circular cutout.
In this guide, we’ll examine precisely how a hole saw works, offer a few basic tips on how to use a hole cutter bit properly, and also look in more detail at some of the many different versions of job-specific hole saws you can buy on today’s market.
How does a hole saw work?
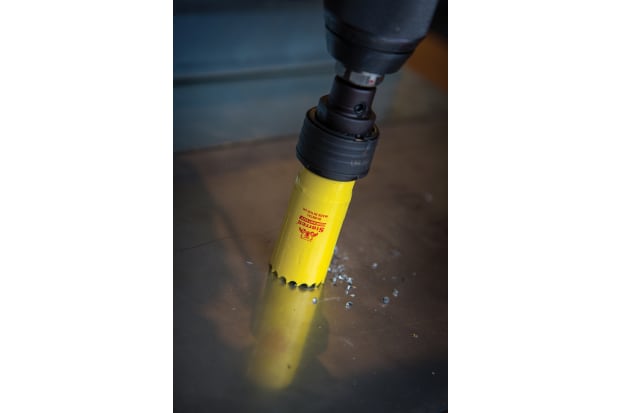
As implied by the name, a hole saw is made to cut a circular hole of much wider gauge through a workpiece than standard drill bits can create on their own. As with most power tool accessories, the key to choosing a high-end, well-made hole cutter is to look out for a combination of robust construction, quality materials and accurate, tidy machining.
Specifics such as tooth design and overall shape will vary depending on what material the hole saw in question is intended for use on, but almost all products supplied by reputable hole saw brands will have a few traits on common.
As a general rule, the cylindrical walls of a good hole cutter bit are deliberately manufactured to be rather thin in relation to the overall internal diameter of the tool. This helps to reduce friction between the teeth and the work surface, and in turn means less user force is required to break through a workpiece, putting less strain on the drill’s motor as the hole is drilled.
The diameter of the hole created will depend on the rated width of hole saw you purchase. Usually these holes will be made in some form of sheet material - see the sections below for specific examples and applications - although hole saws can also be purchased at varying lengths/depths as well as different diameters. Buying a deeper hole saw bit may allow for clean circular cuts through even fairly thick materials (provided the drill in question is properly set up and specced to handle them safely, of course).
Many hole saws and hole saw kits therefore come with arbors or pilot drill bits pre-packaged as an extra feature, but almost all are compatible with standard arbors and other hole saw accessories if not. Other optional features found in certain types of application-specific hole saw bits might include:
- Diamond tips for use on ceramics and masonry
- Extra heavy duty construction for tougher jobs or materials
- Carbide-tipped teeth for use on fibreglass, formica, galvanised iron etc
- Extra thin kerfs (i.e. tooth thickness) for fast and easy cutting
- A raised shoulder around the base of the hole cutter, designed to help prevent overdrilling/breakthrough in cases where this isn’t the desired result
How to use hole saws?
When dealing with different sorts of materials (including natural and engineered timbers, glass, plastic, ceramics and metal), you’ll most likely need to choose different types of hole saws - and often employ slightly different drilling techniques - in order to achieve the neat, clean-cut, professional-looking results you’re after. While collections of guidelines are seldom any match for hands-on experience in this department, there are some fairly universal techniques and basic user tips that all hole saw operators should bear in mind when approaching a new job.
Always make sure you’re using an appropriately powerful drill for hole cutting
Cordless models can get the job done on thinner or softer materials, but you’ll require at least a 14V model
You should never attempt to bore holes through masonry or heavier timber (anything over about 50mm) with a battery-operated drill
Always equip yourself with suitable PPE safety wear before starting to use a hole saw
As a minimum, this should always include suitable goggles or glasses, an appropriate dust mask for the material being cut, and good quality work gloves
Never wear loose clothing - such as baggy sleeves or dangling jewellery - that could get snagged in the hole saw, and always tie back long hair securely
Regardless of the material or surface you’re working on, never try to force the drill bit through any faster than it wants to go
Gentle, consistent pressure is key to achieving a neat, perfectly round hole
Always start off slowly and gradually increase rotation speed as you go
Apart from the power rating of your drill, the main limiting factor in terms of hole depth will often be the specific design of the hole cutter, and in particular the way it’s set up to deal with the material being removed:
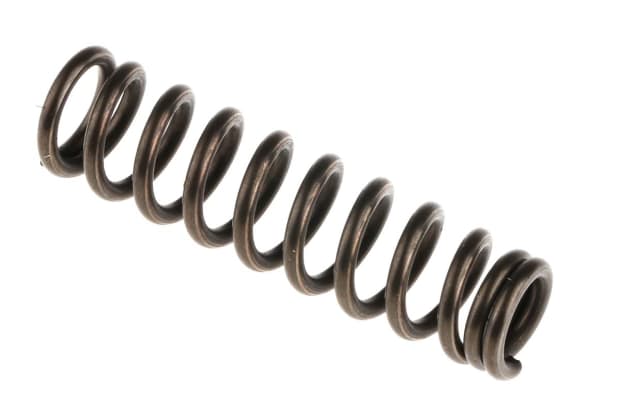
Typically, a plug or buildup of removed material will amass inside the hollow core of the hole saw, eventually blocking and preventing it from descending beyond a certain depth (stated alongside diameter under the manufacturer’s product specifications)
At this point, the user may need to clear out the build-up using a screwdriver or similar ‘poking tool’
In many cases, it’s possible to do this via the handy ‘speed slots’ that many brands cut into the side walls of their hole cutters for this very reason
More advanced designs might feature an ejector spring for this purpose, usually wound around the central arbor if one is present - you can also buy ejector springs (pictured on the right) as an aftermarket hole saw accessory
However, in cases where no such springs or clearout slots are available, you’ll need to lift the cutter away from the workpiece and manually empty out the hollow core from the open end before continuing
Ensure you cut directly down into the workpiece at an accurate perpendicular (90-degree) angle to the surface
This is the best way to prevent binding and sticking of the hole saw, or even stalling/burning out the drill’s motor
Be aware that going in at a slightly off-centre angle - or hitting a nail while drilling - can cause very sudden and violent binding/jamming of the drill when using a hole saw
Check that the full perimeter of the hole saw cutting edge is making even contact with the work surface all the way around before you start drilling
When making large-bore holes in most types of sheeting and solid materials, it’s always advisable to use an arbor or pilot hole of some kind, in order to prevent the hole cutter from skidding around on the surface during the initial stages of the cut
Whether included as part of a hole saw kit or purchased separately, these pilot bits sit at the centre of the hole saw’s hollow cylinder, and are usually removable or adjustable (often with a suitable hex or Allen key provided)
They will generally extend anywhere from 10-30mm out beyond the open cutting end of the hole saw, and may also incorporate an ejector spring mechanism for helping to jettison plugs of loose material build-up
If you want to drill a hole clean through a workpiece, be aware that going directly from one side through to the other with a hole saw can create a lot of ‘blowout’ (material tearing) on the reverse side
This is due to the width of the hole cutter bit, and the subsequently large amount of material being removed
To counter this, a good technique is to wait until the arbor or pilot bit breaks through - then move to the rear side (if accessible) and drill back the way you came, to a depth of a few millimetres, using the pilot hole as a guide
Once you’ve done this, return to the starting side and complete the full depth of the hole cut
One common hole saw problem encountered on many job sites and DIY projects is needing to drill a larger hole in place of an existing smaller one - for example, when fitting a new halogen downlight of wider diameter than the previous model
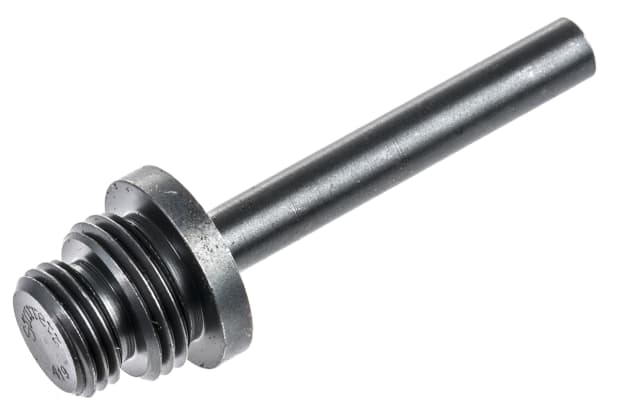
This is tricky, as there’s typically nowhere to seat the arbor or pilot bit in order to begin the cut cleanly and steadily
If the rear side and edges of the workpiece are accessible, clamping a scrap piece of timber behind it can give you a surface to drill your pilot hole into
Where this isn’t possible, a very handy optional accessory would be something like a hole saw re-work adapter (pictured on the right), which allows the user to attach two different diameters of hole saw bits simultaneously
The smaller hole saw thus acts as the guide or arbor bit (sized to the existing hole width), and the larger attachment then cuts a new, bigger hole around it
Consider using an accessory such as a dust cowl to cover the hole saw bit while in use, and prevent excessive spillage of debris when boring out large holes
These simple add-ons also help to protect the drill itself by stopping dust from directly entering the motor, especially when working overhead
Dust covers and cowls generally work by accepting the shank of the arbor through a central hole, and flexing as you drill to allow better access to the work surface
Once the hole has been drilled, all the dirt and debris is collected in the cowl for easy and tidy disposal
Applications and types of hole saws
As we’ve already touched on in this guide, there are many different types of hole cutters and hole saw accessories available for various sorts of applications and working environments. These might typically include, to name just a few:
Drilling holes for cable routing and wiring runs
Making cutouts in ceilings for placement of downlights, fittings or light fixtures
Fitting taps and other hardware to sinks, baths and worktops
General joinery, woodworking and DIY projects
Fitting conduit runs or drainage pipes through kitchen units and walls
Installing hardware for doors and cabinets, including handles, locks and rails
Boring through masonry for improved ventilation or waste removal purposes
Hole saws for metal
Hole saw cutters for sheet metals are generally manufactured to be extra robust, and can withstand the much higher temperatures generated by cutting through a range of common metals such as (stainless) steel.
While these sorts of tough working conditions don’t often cause an immediate or catastrophic failure in other types of hole saw bits, they can degrade the product relatively quickly if it wasn’t designed for the job, making them much less cost-effective over time. As a result, carbide-tipped teeth are a feature to look out for on hole cutters intended for metal working.
You’ll find these widely available on products released under many leading brand names - the question of who makes the best circle cutter bits is a subject for much debate, but common nominations for the title often include both Starrett hole saws and Lenox hole saws.
Hole saws for wood
Most multi-purpose, universal or bi-metal hole saws will get the job done on most types of timber and sheet wood - although for extra efficient and tidy cutting of engineered woods such as MDF, you may also like to consider a brand that offers carbide-tipped teeth.
As noted above, these are typically chosen primarily for cutting holes in metals, but they can also offer a handy edge when you’re working with timber derivative materials that are likely to produce excessive dust or debris or toxic fumes (particularly as the temperature builds up during use, which can quickly start to melt composite adhesives).
Hole saws for glass
Hole cutters manufactured for use on glass and ceramics - as well as models intended as stone, brick and concrete hole saw bits - will often feature gulleted or square teeth, set further apart than you’d typically find on timber or plastic hole saws. This delivers more brute power to these harder or more abrasive cutting surfaces, at the cost of a somewhat less neat hole.
Hole saws for concrete
Generally speaking, the teeth on most masonry hole saws (sometimes referred to as ‘core drill bits’) will be more widely spaced than timber versions, and often diamond-tipped teeth for extra hardness and cutting power.
This wider spacing makes it easier for removed material to fall away from the hole saw edges, helping to prevent clogging and binding. You may also see ‘variable pitch’ hole saws on sale for similar heavy-duty workloads - this indicates an irregular distance between teeth, and can help lower overall vibration/noise, eject removed material faster, and reduce overall wear on the tool. Again, the trade-off is a slightly rougher hole.
Hole saws for tile
An alternative configuration of hole cutter designed for use on ceramic tile, porcelain, glass and masonry is the toothless or ‘coated’ hole saw. Rather than having jagged or crenellated teeth protruding from the cutting edge, these types of hole saws instead feature a flat rim that’s coated with a hard, abrasive material such as diamond or carbide.
The key advantage of the toothless or fast-cut hole saw design is that it allows for neater, finer, speedier cuts to be made in very hard or dense materials with less risk of chipping and breaking. They may sometimes require some form of water-cooling to be applied in use, as the increased friction area can generate excessively high temperatures.
Related links
- Hole Saws & Core Drill Bits
- The Complete Guide to Screwdriver Bit Sets
- The Complete Guide to DIP Switches
- The Complete Guide to Torches
- The Complete Guide to Stepper Motors
- The Complete Guide to OLED Displays
- A Complete Guide to Uninterruptible Power Supplies (UPS) by Eaton
- The Complete Guide To Lighting Ballasts