- Published 25 Mar 2024
- Last Modified 25 Mar 2024
- 8 min
Understanding Conveyor Parts and Maintenance to Boost Mining Operation Efficiency
Discover how to enhance mining efficiency with RS's conveyor solutions. Learn maintenance tips for seamless operations and quality parts to consider.

Australia has cemented its position as a leading force in the global mining sector, renowned for exporting critical resources like coal, iron ore, bauxite, and alumina. And according to Statista, over the past decade, this industry has made significant contributions to the nation's economy, with its gross value totalling billions of Australian dollars, representing more than 10% of Australia's total gross value added. This highlights its pivotal role as a primary economic driver. This substantial contribution underscores the paramount importance of operational efficiency within the industry.
However, the logistical and transportation demands within mining operations are notably intricate and diverse, influenced by factors such as mine location and supply chain complexities. Despite these challenging aspects, specific tools and equipment have been proven integral to both surface and underground mining activities. Some of these include heavy-duty vehicles like mining trucks, loaders, and haulage carriers that are leveraged for tasks like transporting run-of-mine (ROM) ore to processing sites.
And at the core of these types of logistical operations lies the conveyor belt system.
Widely utilised across industries, even beyond that of the mining sector, conveyor belts offer solutions to numerous logistical problems, enabling efficient material transport over short and long distances, steep inclines, and gradual declines.
Narrowing in on the mining sector, these systems are critical for effectively moving ores, concentrates, and tailings, seamlessly integrating into the continuous material handling processes essential for mining efficiency and productivity. But how can you ensure that they operate at peak efficiency and sustain the high productivity levels crucial for the mining industry's success?
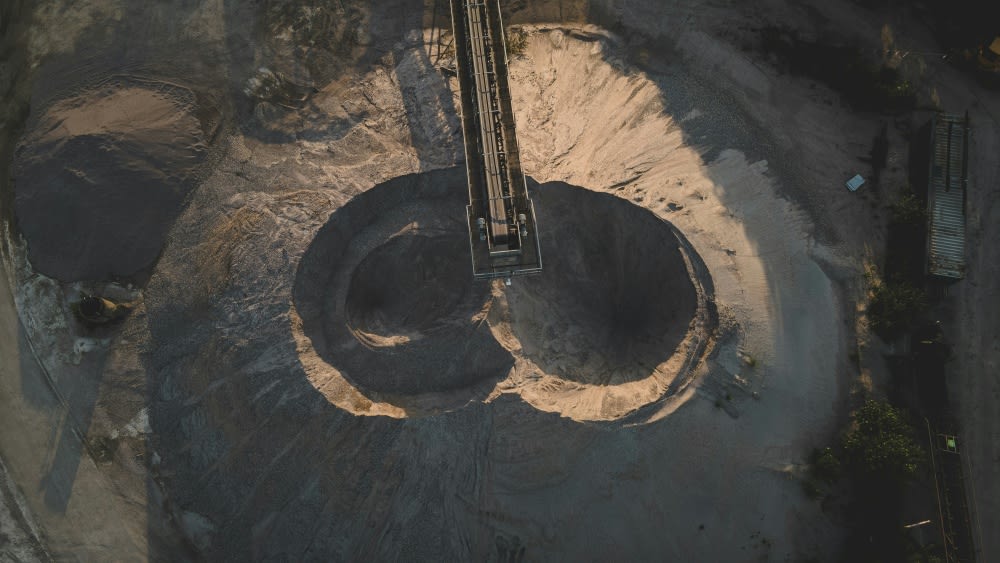
Components and Parts of Conveyor Systems Used in Mining
Conveyor systems in the mining sector are engineered to accommodate a wide spectrum of operational needs, ranging from the straightforward to the intricately complex. Therefore, it is safe to say that the diversity in mining operations, dictated by the variety of products extracted, directly influences the design and functionality of these conveyor systems. This variety extends to the components that make up the systems.
Central to these systems are several key components:
1. Belt
The conveyor belt, a critical component within mining operations, is available in an array of configurations to suit various transportation tasks. Options include smooth rubber belts, ideal for the general purpose of moving goods horizontally, and chevron belts, designed to prevent slippage on inclines. For heavier or more demanding loads, steel-reinforced belts offer enhanced durability, safety and flexibility. Belts equipped with sidewalls and bins are tailored for specific material and load handling needs at a maximum slope, while tubular conveyor belts are utilised for enclosed transport, protecting the materials from environmental contaminants and reducing loss.
Beyond these belt types, the mining industry also leverages alternative conveyor systems to meet unique operational requirements. For example, screw conveyors are employed for precise handling of granular or powdered materials, offering controlled feeding and discharge. Drag chain conveyors, on the other hand, are chosen for their robustness in moving heavy, abrasive materials, showcasing the versatility of conveyor solutions in adapting to the diverse needs of mining operations.
2. Rollers and Idlers
Rollers and idlers are essential conveyor components. Rollers, mounted on bearings, propel materials efficiently using gravity and minimal power. Idlers, on the other hand, evenly distribute weight across the belt, enhancing performance and longevity. These parts of the conveyor reduce friction and wear, boosting mining operation efficiency.
3. Support Structures
Efficient conveyor belt operation relies on sturdy support structures to prevent sagging and ensure smooth movement. A well-designed system includes a durable frame, legs, and cross members for stability, along with accessories like scrapers to enhance performance and minimise maintenance needs.
4. Driving Unit
The conveyor's core lies in the drive unit, comprising a motor bracket, counter-bearings, and an electrical drive. This unit ensures smooth operation, facilitating continuous movement and direction adjustments. It offers control over speed and direction, enhancing productivity, energy efficiency, and safety in mining operations.
5. Conveyor Motor
Conveyor motors, available in AC and DC types, match diverse operational needs with options for power, speed, and torque. Linked to gearboxes or conveyor components, they're controlled via variable frequency drives for precise speed and direction. Known for robust performance, low maintenance, and energy efficiency, they minimise downtimes and operational costs while offering easy installation and repair.
How Do These Components Work Together to Facilitate Transportation?
The seamless operation of a conveyor system in mining hinges on the harmonious interaction between all the aforementioned core parts. Each element plays a distinct role in ensuring efficient material transport.
For example, the belt moves materials, guided by rollers and idlers, while support structures maintain stability. The drive unit and electric motor then work to provide power, enabling controlled movement for optimal material flow.
This cohesive system minimises downtime and boosts productivity across mining operations—that is, if the conveyor system is well-maintained.
The Importance of Conveyor System Maintenance
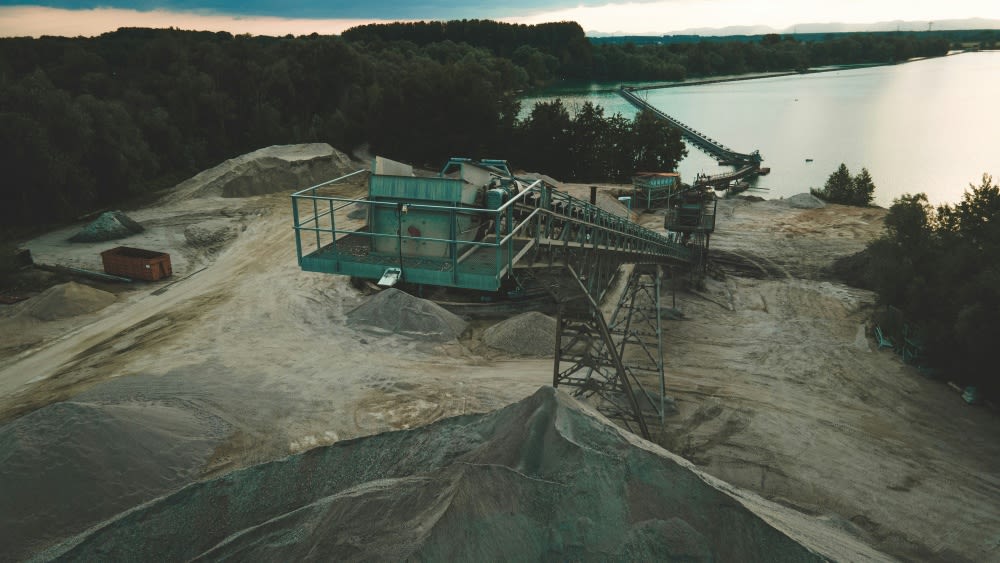
In light of the Australia Conveyor Maintenance Market's projections, which anticipate a moderate compound annual growth rate (CAGR) of 2.9% through 2032, reaching an expected valuation of US$ 873.43 Million, the emphasis on diligent conveyor maintenance in the Australian mining sector has never been more critical. This growth underscores the vital role of regular maintenance and inspections in safeguarding the longevity and reliability of conveyor systems.
Common Issues Related to Conveyor Systems
Conveyor systems, being intricate configurations of various technological and mechanical components, necessitate periodic and skilled care to ward off wear, tear, and functional discrepancies. Common pitfalls include belt misalignment, wear on rollers, and malfunctions in the chain mechanism. Similarly, electric motors integral to these systems are prone to overheating, bearing failures, and electrical faults if not meticulously maintained.
Failure to address these issues in the intricate mechanical systems of the conveyor can lead to prolonged downtime, reduced productivity, and higher repair costs. But beyond mere operational efficiency, regular maintenance is also a must to ensure a safe working environment. This is because poorly maintained conveyors can present serious safety hazards, potentially leading to accidents or injuries.
Proactive maintenance can thus help detect and resolve issues early, preventing the occurrence of major problems.
Best Practices in Conveyor System Maintenance
To ensure the smooth operation of electric motors within conveyor setups, it's advisable to adhere to maintenance practices like routine lubrication, checks on features like safety guards and thorough inspections of electrical connections. Such measures not only enhance the reliability of conveyor systems but also contribute to their efficient performance.
Listening for unusual noises from the motor during operation, monitoring gearbox and motor temperatures, and keeping an eye on the condition of bearings and idlers should all be part of a thorough maintenance regimen.
Such practices not only mitigate the risk of safety incidents but also bolster production efficiency and facilitate significant cost savings over time, ensuring conveyor systems operate optimally and safely.
Upgrading and Enhancing Conveyor Systems
Since conveyors are pivotal in transporting heavy materials across various stages of processing, it should come as no surprise that the quality of system components directly influences overall performance. This is where the integration of superior-quality parts can significantly impact the productivity and reliability of mining operations. Beyond elevating operational efficiency, it can also extend the lifespan of the equipment involved.
Understanding this need, RS stands at the forefront of supplying high-grade components that cater specifically to the demanding nature of the mining industry. So, how do you go about upgrading your conveyor system with high-quality parts?
Firstly, giving attention to selecting the right electric motors is crucial, especially since their central role is in driving the conveyor. Motors that are specifically designed to withstand the rigorous conditions of mining operations, along with compatible pulleys that facilitate load movement and reduce system friction, are all instrumental. Additionally, the right combination of motors, rollers, and idlers is key to ensuring seamless operation.
Maximise Conveyor System Efficacy with RS
When it comes to mining operations, the integrity and functionality of conveyor systems are paramount. Recognising this, RS offers an extensive selection of conveyor parts, including small electric motors that drive the entire system. Each component is engineered to bolster the efficiency and reliability of conveyor systems, ensuring that materials are transported smoothly across mining operations.
Delve into our comprehensive range of conveyor parts, as well as other mining solutions like mining PPE and professional hand tools for mining and discover how our premium parts can enhance the safety, efficiency, and reliability of your operations.
With RS as your partner, rest assured you'll be equipped with the tools and support necessary to elevate your conveyor system to new heights of operational excellence.
Popular Electric Motor Brands
Related links
- The Critical Role of Push Button Switches in Mining Operations
- Variable Speed Electric Motors in HVAC Systems for Energy Efficiency
- Renewables & Energy Efficiency for Business
- The Complete Guide to AC Motors
- The Impact of Servo Motors on Automated Drilling Equipment in Mining
- The Role of Electric Motors in Sustainable Railway Systems
- A Strategic Selection of Power Supplies and Transformers
- Innovative Problem-Solving with Thermal Cameras