- Published 19 Feb 2025
- Last Modified 19 Feb 2025
- 11 min
Guide to Check Valves: Types, Applications & Selection
What does a check valve do? Learn about check valve types, how they work ,what they are used for & how to choose the right one for your needs.

This comprehensive guide provides everything you need to know about check valves, from their basic function and operation to the various types available and their applications across diverse industries. It will equip you with the knowledge to understand and select the right check valve for your needs. We'll explore the different types of check valves, the materials they're made of, and the key factors to consider when choosing one.
What is a Check Valve?
A check valve, also known as a non-return valve or one-way valve, is a self-actuating valve designed to allow fluid (liquid or gas) to flow through it in only one direction. Check valves are two-port valves, meaning they have two openings: one for fluid to enter and the other for fluid to exit. They are typically automatic in operation, meaning they don't require any manual control or external intervention. As such, most check valves are not equipped with a handle or stem.
What Does a Check Valve Do?
A check valve's primary function is to prevent backflow, ensuring that fluids flow only in the intended direction. This helps protect equipment, maintain system pressure, and prevent contamination. Check valves are used for a wide variety of purposes, serving as vital components in applications ranging from household plumbing to complex industrial processes.
Check Valve Diagram
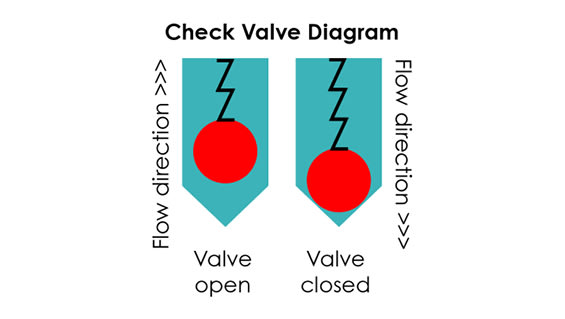
How Does a Check Valve Work?
A check valve operates using a straightforward mechanism. Inside the valve body, there's a movable element, such as a ball or disc, that responds to pressure changes. When fluid flows in the forward direction, the pressure pushes the element open, allowing fluid to pass. If the flow reverses, the pressure pushes the element closed, sealing the valve and preventing backflow. This simple operation ensures unidirectional flow without the need for external controls.
To understand this operation more fully, it's important to consider a few key aspects of how check valves work:
Cracking Pressure:
The "cracking pressure" refers to the minimum upstream pressure required to open the valve. This pressure must be overcome to allow forward flow. Check valves are designed with specific cracking pressures to suit different applications, ensuring they open only when the pressure is sufficient.
Closing:
Check valves close automatically when the flow reverses or drops below the cracking pressure. The closing speed can be a critical factor in preventing pressure surges (water hammer) in some systems. Some check valves incorporate features like springs or dampers to control the closing speed and minimise pressure fluctuations.
Installation Orientation:
Some check valves have specific installation orientation requirements (e.g., vertical or horizontal) to ensure proper operation. For example, swing check valves typically require horizontal installation, while lift check valves can be installed in either orientation. Always refer to the manufacturer's instructions for specific guidance.
Normally Open vs. Normally Closed:
Most check valves are "normally closed," meaning they are closed in the absence of forward flow. This is the most common configuration for preventing backflow. However, some specialised applications may require "normally open" check valves, which remain open until the flow reverses.
Types of Check Valves
Check valves are broadly categorised into two main types: single-check valves and double-check valves. Understanding the difference between single vs double check valve configurations is crucial for selecting the right valve for your application.
Single-Check Valves
Single-check valves are the most common type, using a single moving element to control flow direction. They are suitable for a wide range of applications where basic backflow prevention is required. Here are some common types of single check valves:
Ball Check Valves
Ball check valves use a ball to seal the valve. They are simple, reliable, and often used in low-pressure applications where minimal flow resistance is desired. Ball check valves are commonly found in applications like spray devices, hydraulic systems, and small-bore piping.
Swing Check Valves
Swing check valves have a hinged disc that swings open for forward flow and closes against a seat to prevent backflow. They are common in larger pipes and offer low flow resistance, making them suitable for applications with high flow rates. Swing check valves are often used in water treatment, wastewater management, and industrial processes.
Lift Check Valves
Lift check valves feature a disc that lifts vertically to allow flow. They are known for precise seating and are often used in higher-pressure applications where tight shut-off is required. Lift check valves are commonly found in applications like oil and gas pipelines, chemical processing, and power generation.
Diaphragm Check Valves
Diaphragm check valves use a flexible diaphragm to seal the valve. They are suitable for low-pressure differentials and are often used in sanitary or corrosive environments due to their smooth flow path and minimal crevices. Diaphragm check valves are commonly used in medical devices, food processing, and chemical handling.
Tilting Disc Check Valves
Tilting disc check valves use a disc that tilts to open or close. They offer good flow characteristics and are suitable for applications with pulsating flow, minimising pressure drops and reducing the risk of water hammer. Tilting disc check valves are often used in pump systems, HVAC systems, and industrial processes with fluctuating flow rates.
Piston Check Valves
Piston check valves are similar to lift check valves but use a piston-like element. They are robust and suitable for high-pressure applications where durability and tight sealing are essential. Piston check valves are commonly used in hydraulic systems, oil and gas applications, and high-pressure water systems.
Butterfly Check Valves
Butterfly check valves use a rotating disc to control flow. They are compact and offer good flow characteristics, making them suitable for applications with space constraints. Butterfly check valves are commonly used in HVAC systems, water treatment, and industrial processes.
Double-Check Valves
Double-check valves use two single check valves in series, providing an extra layer of protection against backflow. This configuration is often used in applications where backflow prevention is critical to prevent contamination or ensure public health, such as in potable water systems and pharmaceutical processing.
What Are Check Valves Made Of?
Check valves are manufactured from various materials to suit different applications and fluid compatibility requirements. The choice of material depends on factors such as the fluid being handled, operating temperature and pressure, and the required level of corrosion resistance.
Stainless Steel
Stainless steel check valves are highly durable and resistant to corrosion, making them suitable for harsh environments and aggressive fluids. They are often used in high-temperature and high-pressure applications, such as in chemical processing, oil and gas, and industrial manufacturing. Stainless steel check valves are available in various grades, with 316 stainless steel offering enhanced resistance to chlorides and other corrosive substances, making it suitable for marine and coastal applications.
PVC
PVC check valves are lightweight, cost-effective, and offer good chemical resistance. They are resistant to most corrosive media, including seawater, acids, bases, chloride solutions, and organic solvents. However, they are not suitable for use with aromatic and chlorinated hydrocarbons. PVC check valves are commonly used in water treatment, irrigation, and some chemical processing applications where corrosion resistance and affordability are important. They typically have a maximum temperature resistance of around 60 °C.
Brass
Brass check valves are versatile and suitable for use with air, water, oil, and some fuels. They offer good corrosion resistance but are not ideal for seawater or chlorinated water. However, compared to stainless steel, brass is less resistant to corrosion and heat. Brass check valves are thus often only used in plumbing, HVAC, and pneumatic systems where moderate pressure and temperature requirements are met.
Check Valve Symbol
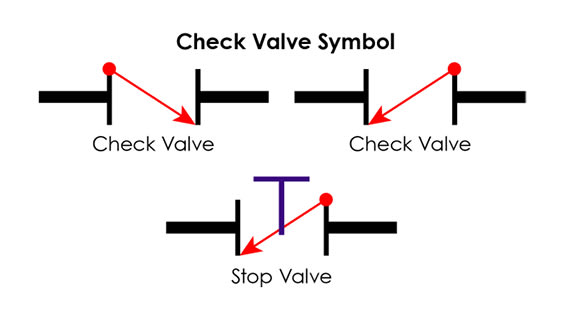
Check valves are represented by specific symbols in piping diagrams, known as Piping and Instrumentation Diagrams (P&ID). The check valve symbol typically shows an arrow indicating the allowed flow direction with a line across it to signify backflow prevention. The non-return valve symbol and the check valve hydraulic symbol are essentially the same, representing the same functionality. These symbols help engineers and technicians quickly understand the function and flow direction of check valves within a system, facilitating efficient design and maintenance.
Industry Applications of Check Valves
Check valves are essential components in numerous industries, playing a critical role in maintaining safety, and efficiency, and preventing contamination. For instance, check valves are crucial in centrifugal pumps, ensuring that water keeps flowing in the right direction until the air within the pump has been expelled, preventing damage and ensuring efficient operation. Similarly, in Heating, Ventilation and Air Conditioning (HVAC systems), especially in larger buildings where coolant needs to be pumped to multiple floors, check valves prevent backflow, ensuring that the coolant circulates effectively and maintains the desired temperature.
Here are some key industries where check valves are extensively utilised:
- Oil and Gas: In the oil and gas industry, check valves are crucial for preventing backflow in pipelines and ensuring the safe and efficient transport of hydrocarbons. This helps prevent contamination, equipment damage, or accidents. They are also often used alongside pressure-reducing valves (PRV) to regulate pressure in pipelines, refineries, and other facilities, ensuring safe and efficient operation.
- Water Treatment and Distribution: Check valves are vital in water treatment plants and distribution systems to prevent contamination of clean water supplies. They ensure that treated water flows in the desired direction and prevent backflow from potentially contaminated sources.
- HVAC Systems: HVAC systems rely on check valves to control the flow of refrigerants, air, and water. They ensure proper circulation and prevent backflow, which can disrupt system operation and damage components. Check valves are commonly used in chillers, air handling units and heat exchangers.
- Power Generation: Check valves play a critical role in power generation facilities, including thermal, nuclear, and renewable energy systems. They regulate the flow of steam, water, and other fluids in turbines, boilers, and condensers, ensuring efficient operation and preventing damage.
- Pharmaceutical and Food Processing: In pharmaceutical and food processing, maintaining hygiene and preventing cross-contamination is paramount. Check valves ensure unidirectional flow of ingredients and fluids, preventing backflow that could compromise product quality or safety. These valves are commonly found in processing equipment, filling machines, and packaging lines.
- Automotive and Aerospace: Check valves are used in automotive and aerospace applications to control the flow of fuel, oil, and hydraulic fluids. They prevent backflow, ensuring that fluids move in the intended direction and protect critical components, such as in fuel systems, braking systems, and hydraulic systems in vehicles and aircraft.
How to Choose the Right Check Valves
Choosing the right check valve is crucial for optimal performance and preventing problems in your system. Since different applications have unique needs, there's no one-size-fits-all solution. You'll need to carefully evaluate several factors to ensure you select a check valve that provides reliable performance, requires minimal maintenance, and offers long-term efficiency. These factors, while not always equally important, should be considered in relation to your specific system requirements.
- Fluid Compatibility: The valve materials must be compatible with the fluid being handled to avoid corrosion, degradation, or contamination. Consider the chemical properties of the fluid, temperature, and potential for abrasive particles.
- Flow Characteristics: Evaluate the flow rate, pressure, and potential for pulsations in the system. Choose a valve that can handle the flow dynamics without excessive pressure drop or risk of water hammer.
- Head Loss: Head loss refers to the pressure drop across the valve due to flow resistance. Select a valve with minimal head loss to maintain system efficiency and minimize energy consumption.
- Total Cost of Ownership: Consider not only the initial purchase price but also the long-term costs associated with maintenance, repairs, and potential downtime. Choose a durable and reliable valve to minimise lifecycle costs.
- Non-Slam Characteristics: In applications where rapid valve closure can cause pressure surges or water hammer, consider valves with non-slam features. These features, such as dampers or slow-closing mechanisms, help to mitigate pressure fluctuations and protect the system from damage.
By carefully evaluating these factors and considering the specific requirements of your application, you can choose the right check valve to ensure reliable performance, minimal maintenance, and long-term operational efficiency.
Check valves are essential components in a wide range of fluid systems, ensuring safe, efficient, and reliable operation by preventing backflow. Understanding the different types of check valves, their applications, and the key factors to consider when selecting one is crucial for engineers, technicians, and anyone working with fluid systems. By choosing the right check valve and ensuring proper installation and maintenance, you can optimise your system's performance and prevent costly downtime or damage. Check out our other guides on rheostats, fuse types and more, and if you have any further questions or need assistance in selecting the right check valve for your specific needs, don't hesitate to contact our experts at RS AU.
Related links
- Hydraulic Check Valves
- Check Valves
- RS PRO Stainless Steel Hydraulic Check Valve 90L/min
- RS PRO Steel NPT 3/8
- Exploring the World of Cable Joints: Types and Applications
- Parker Steel Inline Mounting 2301 20L/min, 0.35bar Cracking Pressure
- RS PRO Stainless Steel Hydraulic Check Valve 110L/min
- Parker Steel Inline Mounting 2305 150L/min, 0.35bar Cracking Pressure