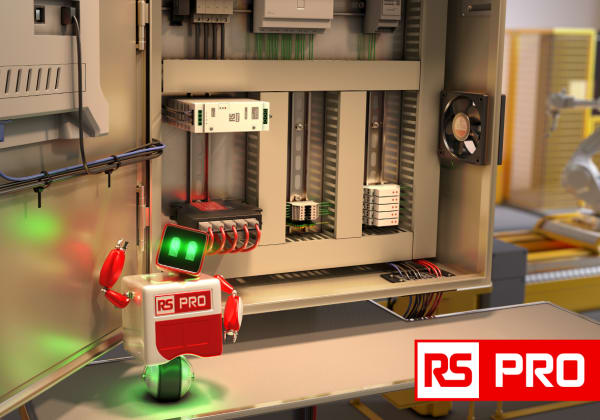
Your Smart Choice for Electrical Control Panels
Everything from Power Supplies to Push Buttons - RS PRO has the parts you need to build, maintain or level-up panels.
Inspiration, information and insight from RS
Everything from Power Supplies to Push Buttons - RS PRO has the parts you need to build, maintain or level-up panels.
We're by your side with a wide range of products to suit the demanding environments of your industry. Find the latest articles, innovative new products, service solutions and more related to your industry.
Want to build a better world? We do, which is why we’ve made it easier to find more sustainable products from across our product offer.
We'll help you find your bearings, belts, pneumatics… and a whole lot more - all in one place.
From Head-to-Toe, we can protect you. PPE products and solutions to keep your people safe.
With 80+ years in electronics, we're your go-to for products, services, and design tools. From board components to displays, we've got all you need for success.
Shop 50,000+ locally stocked products for next day delivery.
We are working with market-leading partners to ensure that you access the latest technology and innovations.