Everything You Need To Know About Twist Drill Bits

This guide looks at what twist drill bits are, how they’re used and what's currently available on the market for a range of job and project requirements.
What are twist drill bits?
A twist bit is arguably the ‘classic’ drill bit we all tend to picture when we think about tools for general purpose, non-specialist drilling applications. As such, the overall category of twist drill bits covers a fairly broad range of cutting tools, add-ons and accessories.However, although there are several different twist drill bit subtypes, the fundamental design of all twist bits is similar. The main thing that defines a twist bit from all other categories of drill bit is its shape - twist bits are instantly recognisable thanks to their familiar helix or spiralled fluted profiles.
Twist bits are certainly among the most heavily manufactured, commonly used and widely available drilling tools manufactured today. Most professional or hobbyist users that own an electric drill or drill-driver - be it cordless or mains powered - will likely own at least one twist bit to go in it.
Again, while there are a number of different sorts of twist drill bits for use with various different materials and specific applications, all bits of this type share a few key characteristics between them. In addition to the helical flutes running around a cylindrical shaft, twist drill bits also feature some form of cutting tip at one end, and any of various types of shank at the other (for insertion into the drill chuck).
The history of twist drill bits
Morse’s initial concept was to improve the ease and accuracy of drilling holes by producing a drill bit that began from a sharpened point, with fluting along the sides of the shaft that would help push the cut material (swarf) back out of and away from the hole as it went.
To do this, he patented an early manufacturing process whereby he’d cut two grooves in opposite sides of a cylindrical metal bar, and then twist the bar under heavy torque to produce the now-familiar spiralled or helix double flutes. Although the actual mechanics of production have since been extensively mechanised and streamlined, Morse’s initial twisting method of creating the helical grooves is what gives this style of drill bit its name to this day.
How are twist drill bits made?
Modern manufacturing processes for twist drill bits actually involve clamping a steel bar (or occasionally some other material, in the case of a few specific product types) in a vice or similar assembly, and rotating it at high speed while moving it past a suitably calibrated grinding wheel.During the manufacture of a twist drill bit, the axis of the grinding wheel can be angled to varying degrees, in order to achieve a particular angle of fluting around the shaft of the drill bit. A helical angle of between 28-32 degrees is a universal standard for almost all twist drill bits, and is broadly deemed suitable for use on the majority of general purpose drilling work and materials.
However, certain specialised applications or materials can benefit from slightly different fluting angles, and a number of non-standard twist drill bits are manufactured for such purposes. Examples might include:
Fast spiral twist bits
- This type of twist drill bit has a higher helical angle than standard, usually somewhere between 34-38 degrees
- The higher angle of the fluting on a fast spiral bit makes it better at ejecting swarf, chips and other forms of removed material, which is important when drilling through certain tougher surfaces or when drilling significantly deeper holes
Low helix angle bits
- Conversely, some relatively soft work materials - including certain sheet products and a variety of softer metals (notably brass and bronze) - can benefit from the use of a twist drill bit with lower than standard fluting angles, generally set between 12 and 22 degrees
- A lower helix angle makes a twist drill bit less likely to pull ahead as you feed them into the hole, or to grab on exit - reamers are also a good example of a cutting tool designed with low-angle flutes (or zero angle, in some cases) for this purpose
Long twist drill bits
An especially long twist drill bit will generally be necessary to complete everyday tasks such as these, but the main potential disadvantage of an extra long drill bit is that it can tend to wander more as it goes. Longer twist bits are also more prone to breaking at lower gauges than short bits, particularly when more force is applied to get through greater depths of material.Twist drill bits are also available in a short form.
Reverse twist drill bits
A reverse twist drill bit does exactly what the name implies. It’s designed to work with your drill set to the reverse rotation direction (counter-clockwise) - although unlike a standard drill bit, which would simply drag its cutting edge backwards around the interior of the hole with the drill running backwards, reverse twist drill bits are machined with their fluted cutting surfaces facing in the opposite direction.This means that when a reverse bit is inserted into a chuck and the drill is run counter-clockwise, the bit performs the same sort of cutting action that a standard drill bit does when moving ‘forward’ (clockwise). This can be extremely useful as a method of screw extraction when the slots on a screw head have been worn away or destroyed - and reverse bits are also commonly known as ‘left-handed’ twist drill bits, for obvious reasons!
High speed twist drill bits
The vast majority of twist drill bits are made from high grade steel, of which two particular formulations are especially common for specific scenarios:HSS, or high-speed steel
- High speed twist bits are effectively a universal type of drill bit, and most types of HSS twist bits will be suitable for general drilling work.
- HSS twist bits are a requirement for drilling through various sorts of metallic workpieces and surfaces, as they’re formulated to withstand the higher temperatures generated through the increased friction involved in drilling metal without losing hardness (temper)
Carbon steel
- Conversely, if you’re only going to be drilling through wood, you can instead opt for a carbon steel twist drill bit
- Carbon steel twist bits tend to be less flexible and more prone to breaking under higher torque forces and temperatures than HSS versions, but drilling most types of wood and composite lumber materials is unlikely to cause this issue
- Although more brittle and less robust than HSS bits, especially under higher working temperatures, carbon steel twist drill bits are typically a good deal cheaper than HSS versions, and can prove a more cost-effective option for occasional, exclusively wood-based drilling applications
Other excellent options for increased hardness and drilling speeds include both carbide-tipped and cobalt steel - note, though, that very hard cobalt steel bits in particular requires a degree of skill to use economically, as they’re relatively brittle and can be prone to breaking with indelicate treatment.
Twist drill bit sizes
When buying twist drill bits, the bit sizes stated by the manufacturer guidelines or supplier specifications will always refer to both the length and the diameter of the drill bit body.For the majority of typical professional and hobbyist uses, the maximum size twist drill bit you’re likely to find in most drill bit sets will likely be around 25mm-30mm. Unless you’re taking on lots of particularly heavy-duty jobs, it’s generally far more common to use a range of smaller and shorter twist drill bits for many of the applications you’d need to tackle around the home.
Note that bit size can be stated in either imperial (millimetres) or metric (1/32-inch, 1/2 inch and so on), and the majority of twist drill bit sets for sale on today’s market will contain a good range of sizes for tackling most sorts of day-to-day jobs. Small twist drill bits will most often be useful for precision drilling jobs, or of course for installing smaller, more intricate fixtures, fasteners and hardware.
You should also be aware of the required twist drill bit shank size for the drill you’ll be using on the job. Generally speaking, most household cordless drills will have a 10mm (or 3/8 inch) upper chuck size, but larger and more powerful drills will often be able to accommodate larger shank sizes for using bigger and longer bits.
If you’re routinely going to be drilling very deep or wide-bore holes, it’s advisable to look for a drill with a larger chuck to accommodate twist drill bits with thicker shanks.
Shop for twist drill bits
Twist drill bits for metals
As noted in the section above, you can’t typically expect to use a regular steel or carbon steel drill bit designed for cutting through wood when you’re intending to drill in most metals.This is especially apparent when dealing with particularly hard materials and surfaces, such as steel (straight-up steel-on-steel drilling would mean it’s anyone’s guess which will give out first!). However, there is a good range of treated, coated and tipped twist drill bits for metal on the market, all of which are manufactured to offer a more robust cutting tool for tackling those tougher metalworking jobs.
Of these, the most widely available are probably titanium twist drill bits and cobalt drill bits. Like regular high-speed steel (HSS) drill bits, they’re expressly built for the purposes of drilling through metals. The key difference between titanium and cobalt drill bits is that the titanium versions are toughened with a titanium oxide (or titanium nitride, also known as TiN drill bits) coating, while cobalt steel twist drill bits are crafted entirely from solid cobalt steel.
Although the titanium versions are harder thanks to their special oxide coating, this manufacturing process also means that drill bits of this type can’t be sharpened if they dull over time through use on sheet metals.Cobalt steel twist drill bits, on the other hand, can be sharpened as they’re made from a solid piece. They’re also very hard and abrasive, and particularly good for drilling through very hard materials such as titanium, cast iron and stainless steel.
Another good alternative to cobalt steel would be carbide and carbide-tipped twist drill bits, which allow for very high cutting speeds and offer extensive tool life. However, with increased hardness, the trade-off is usually a more brittle product, so you’ll need to assess which is the best cutting tool for your level of experience, the materials you’ll be working on and the longevity you’re looking for when planning a purchase.
Shop for twist drill bits
Top picks
There’s a wide range of twist drill bits to choose from – browse our top brands by clicking the link to view the full product range.
Shop for Dormer twist drill bits
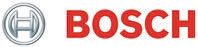
Shop for Bosch twist drill bits
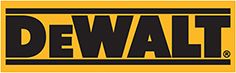
Shop for DeWALT twist drill bits