- Published 19 Apr 2024
- Last Modified 19 Apr 2024
- 8 min
Importance of Contactors & Overload Relays in Mining Electrical Safety
Discover the pivotal role of contactors and overload relays in mining electrical safety. Learn about their functions, importance, and more with RS.

Australia's mining sector stands as a pillar of economic strength, with the Australian Bureau of Statistics reporting a staggering AU$455 billion in export revenue during the 2022–23 financial year. This remarkable figure accounts for two-thirds of the nation's total export revenue. This monumental contribution underscores the industry’s vital role in bolstering Australia's economy, supporting government revenues, and sustaining regional employment.
And given the industry's colossal impact, the imperative to safeguard mining operations cannot be overstated. Hence, ensuring the protection of machinery and maintaining uninterrupted operations are paramount. However, amidst the vast array of hazards present in mining environments, one peril often remains unseen yet is incredibly potent: electrical risks.
While electrical systems are essential to operate an extensive array of mining equipment, from essential tools and lighting to vehicles and heavy machinery, errant currents and faulty conductors pose a severe threat, capable of delivering high-voltage shocks. Plus, in the combustible atmosphere of a mine laden with flammable dust and gases, even a minor electrical spark could lead to catastrophic outcomes.
This is where the critical roles of contactors and overload relays emerge in mining safety.
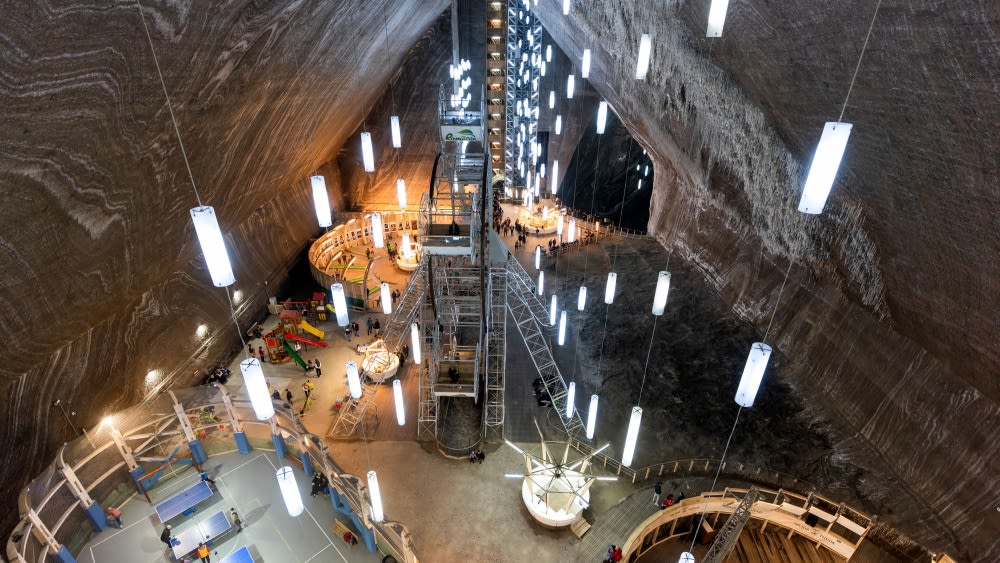
Contactors & Overload Relays: Protecting Mining Equipment
As mentioned, when it comes to mining operations where electrical equipment forms the backbone of day-to-day activities, the importance of maintaining electrical safety cannot be overstated.
This is where contactors and overload relays come in, serving as a fundamental safeguard, protecting equipment from electrical overloads that could lead to costly damages or operational halts. These devices, pivotal in monitoring electrical currents, ensure that the flow remains within safe limits, thereby preserving the integrity and continuity of mining operations.
What is the Difference Between a Contactor and an Overload Relay?
But first, it is essential to understand the difference between a contactor and a relay in managing electrical safety within mining operations.
Contactors, essentially high-capacity switches, are engineered to manage substantial electrical loads. They are the powerhouse behind turning on and off the large electric motors and other high-current applications essential in mining. This capability is due to their design, which includes a coil that, when energised, creates a magnetic field pulling contacts together to complete a circuit, allowing electricity to flow.
Conversely, overload relays serve as critical protective devices designed to sense and respond to electrical overloads that threaten to overheat and damage equipment. Operating on the principle of monitoring, these devices actuate a trip mechanism to cut off power when they detect current exceeding safe operational levels. This ensures the protection of motors and circuits from the potential dangers of electrical overload.
From the above, the primary difference lies in their operational capacity and purpose: contactors facilitate the flow of high currents for powering heavy machinery, using materials optimised for conductivity and techniques for arc suppression to ensure efficiency and safety. Overload relays, on the other hand, focus on monitoring and protection, employing either thermal or electronic mechanisms to prevent electrical overloads.
Together, they form an essential duo in safeguarding electrical systems in mining, ensuring both the operational continuity and safety of the mining environment.
Contactors with Overload Relays in Preventing Catastrophic Outcomes
As briefly covered above, overload relays are designed to meticulously monitor the current flowing through motors, acting as a safeguard against the stresses of overload conditions.
When currents exceed predefined safe limits, the overload relay swiftly triggers, activating an auxiliary circuit. This action effectively cuts off power to the motor by de-energising the contactor, halting the operation and thus preventing damage to the motor windings from excessive heat.
This mechanism is not only crucial for protecting valuable mining equipment from overheating and subsequent failure but also ensures the safety of mining personnel by reducing the risk of fire or electrical hazards associated with overloads.
Optimal Selection and Installation: Keys to Effective Electrical Protection
Understanding that contactors with overload relays are fundamental to mining electrical safety is essential. However, their efficacy in ensuring safety significantly also depends on their appropriate selection and meticulous installation.
Selecting the right devices necessitates a thorough understanding of the specific electrical requirements of mining equipment and the conditions under which they operate. Therefore, factors such as the power rating, the environmental conditions of the mine, and the electrical load's characteristics must be considered to ensure the contactor and overload relay are capable of handling the expected operational demands.
In addition, proper installation goes beyond mere physical placement; it involves integrating these devices into the electrical system in a manner that optimises their functionality and reliability. This involves ensuring that all connections are secure, the settings on overload relays are accurately calibrated to the motor's specifications, and that the devices are accessible for maintenance and monitoring.
The Quest for Zero Harm: Electrical Safety Advances in Australian Mining
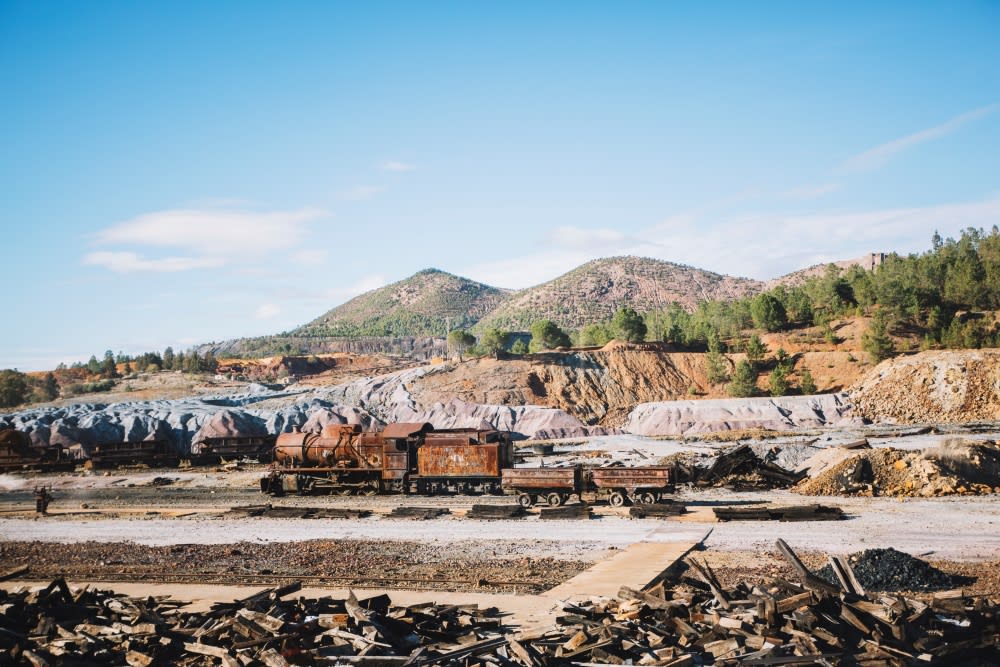
So, why bother striving for the highest standards of electrical safety in mining operations?
The journey towards achieving zero harm in the Australian mining sector underscores the ongoing challenges and the critical importance of vigilance and continuous improvement in safety practices. And despite significant advancements in safety protocols, the risk of electrical hazards remains a pressing concern.
Illustrative of this are recent events, such as the unfortunate incident in a Northern Territory mine where a process operator experienced an electric shock while attempting to address equipment failure during a night shift. Similarly, reports from New South Wales in 2020 of multiple electric shock incidents further underscore the urgent need for enhanced electrical safety measures.
These occurrences serve as stark reminders of the potential dangers that electrical equipment can pose within mining environments, highlighting the indispensable role of contactors and overload relays in fortifying safety and preventing such incidents.
Integration with Mining Safety Systems
Contactor overload relays are not standalone solutions but integral components of the broader mining safety and operational systems.
For example, when incorporated into emergency shutdown systems, contactor overload relays provide a fail-safe mechanism that instantly cuts power to machinery at the first sign of overload or electrical failure. This immediate response is crucial in preventing accidents and minimising the risk of injury, acting on predefined conditions to halt operations without human intervention.
Furthermore, their integration into the mining safety ecosystem allows for seamless communication with other safety components, ensuring a coordinated response to potential hazards.
As such, by functioning as essential elements within automated safety protocols, contactor overload relays enhance the mining industry’s ability to protect personnel and assets.
Challenges and Considerations for Implementation
Despite the list of benefits it brings to the table, there is no denying that implementing contactor overload relays in mining environments presents a set of unique challenges.
For one, the rugged and often remote conditions of mining sites require devices that are not only robust but also compatible with the existing electrical infrastructure. Therefore, one major hurdle is ensuring that these safety devices can withstand the harsh environmental conditions typical of mining operations, such as dust, moisture, and extreme temperatures, without compromising their functionality.
Moreover, selecting the right contactor overload relay involves understanding the specific electrical demands of mining equipment and the nuances of the mine's electrical system. As such, it's crucial to consider the current ratings, the type of load, and the environmental conditions of the site to choose a device that offers reliable protection. Additionally, compatibility with the existing electrical setup is key to avoiding integration issues that could impact system performance.
Enhance Mining Safety with RS
In the rigorous and often perilous world of mining, ensuring electrical safety is not just a regulatory requirement but a fundamental necessity to protect lives and maintain continuous operations. The role of contactor overload relays in this context is indispensable, serving as a cornerstone of modern mining operations' electrical safety measures. These devices, designed to detect and respond to electrical overloads promptly, are crucial in preventing equipment damage and safeguarding against potential operational disruptions and safety hazards.
RS recognises the critical importance of these safety measures and is dedicated to supporting the mining industry's safety needs. We offer an extensive selection of electric motor overload protection devices engineered to meet the diverse and demanding requirements of mining operations. Plus, our portfolio includes solutions designed for durability and reliability, capable of withstanding the harsh conditions characteristic of mining environments.
So, explore our range of overload relays, including thermal overload relays and other safety-enhancing solutions like push button switches for mining operations. With RS, you gain a trusted partner equipped with the expertise and resources to help you navigate the complexities of electrical safety in the mining industry.
Eaton Corporation
Eaton pioneers power management solutions, empowering customers to manage electrical, hydraulic, and mechanical power with reliability and efficiency.